如何正确地进行剪切流变测试
- 关键词:流变学,剪切流场, 剪切流变测试
- 摘要:流变学是研究材料形变和流动(连续形变)的科学,其重要性已在学术界和工业界得到了广泛的认可. 流变仪是研究材料流变性能的仪器,利用流变仪进行流变测试已成为食品、化妆品、涂料、高分子材料等行业的重要表征和研究手段.
2021年,《高分子学报》邀请了国内擅长各种现代表征方法的一流高分子学者领衔撰写从基本原理出发的高分子现代表征方法综述并上线了虚拟专辑。仪器信息网在获《高分子学报》副主编胡文兵老师授权后,也将上线同名专题并转载专题文章,帮助广大研究生和年轻学者了解、学习并提升高分子表征技术。在此,向胡文兵老师和组织及参与撰写的各位专家学者表示感谢。
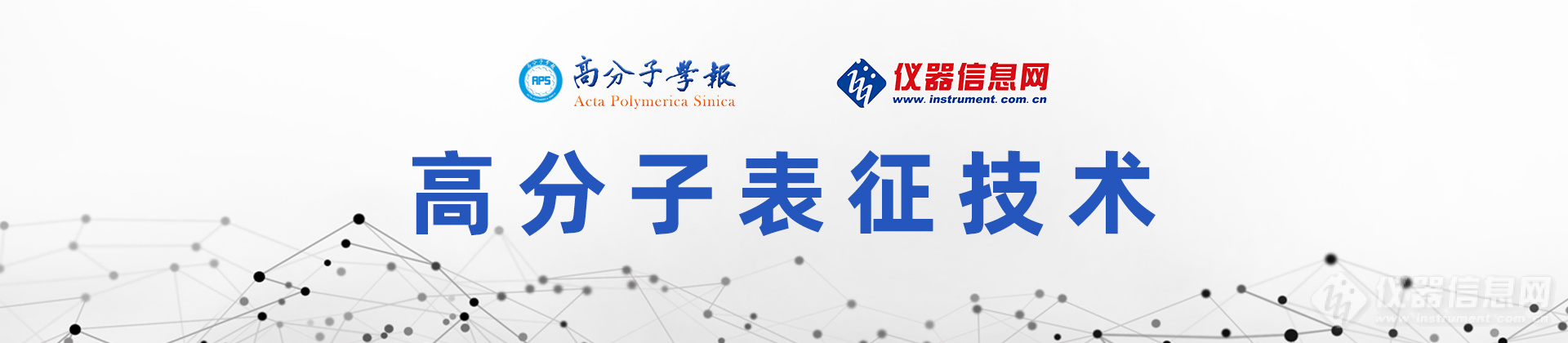
高分子表征技术专题前言
孔子曰:“工欲善其事,必先利其器”。 我们要做好高分子的科学研究工作,掌握基本的表征方法必不可少。每一位学者在自己的学术成长历程中,都或多或少地有幸获得过学术界前辈在实验表征方法方面的宝贵指导!随着科学技术的高速发展,传统的高分子实验表征方法及其应用也取得了长足的进步。目前,中国的高分子学术论文数已经位居世界领先地位,但国内关于高分子现代表征方法方面的系统知识介绍较为缺乏。为此,《高分子学报》主编张希教授委托副主编王笃金研究员和胡文兵教授,组织系列从基本原理出发的高分子现代表征方法综述,邀请国内擅长各种现代表征方法的一流高分子学者领衔撰写。每篇综述涵盖基本原理、实验技巧和典型应用三个方面,旨在给广大研究生和年轻学者提供做好高分子表征工作所必须掌握的基础知识训练。我们的邀请获得了本领域专家学者的热情反馈和大力支持,借此机会特表感谢!
从2021年第3期开始,以上文章将陆续在《高分子学报》发表,并在网站上发布虚拟专辑,以方便大家浏览阅读. 期待这一系列的现代表征方法综述能成为高分子科学知识大厦的奠基石,支撑年轻高分子学者的茁壮成长!也期待未来有更多的学术界同行一起加入到这一工作中来.
高分子表征技术的发展推动了我国高分子学科的持续进步,为提升我国高分子研究的国际地位作出了贡献. 借此虚拟专辑出版之际,让我们表达对高分子物理和表征学界的老一辈科学家的崇高敬意!
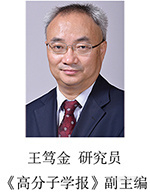
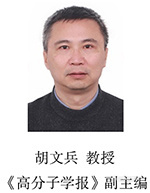
原文链接:
http://www.gfzxb.org/article/doi/10.11777/j.issn1000-3304.2020.20230
《高分子学报》高分子表征技术专题链接:
http://www.gfzxb.org/article/doi/10.11777/j.issn1000-3304
流变技术在高分子表征中的应用:如何正确地进行剪切流变测试
刘双 1,2 ,曹晓 1,2 ,张嘉琪 1,2 ,韩迎春 1,2 ,赵欣悦 1,2 ,陈全 1,2
1.中国科学院机构长春应用化学研究所 高分子物理与化学国家重点实验室 长春 130022
2.中国科学技术大学应用化学与工程学院 合肥 230026
作者简介: 陈全,男,1981年生. 中国科学院长春应用化学研究所研究员. 本科和硕士毕业于上海交通大学,2011年在日本京都大学取得工学博士学位,之后赴美国宾州州立大学继续博士后深造. 于2015年回国成立独立课题组,同年当选中国流变学学会专业委员会委员;于2016年获美国TA公司授予的Distinguished Young Rheologist Award (2~3人/年),同年入选2016年中组部QR计划青年项目;于2017年获基金委优青项目资助;于2019年入选中国化学会高分子学科委员会委员,同年获得日本流变学会奖励赏(1~2人/年),目前担任《Nihon Reoroji Gakkaishi》(日本流变学会志)和《高分子学报》编委;
通讯作者: 陈全, E-mail: qchen@ciac.ac.cn
摘要: 流变学是高分子加工和应用的重要基础,流变学表征对于深入理解高分子流动行为非常重要,获取的流变参数可用于指导高分子加工. 本文首先总结了剪切流变测试中的基本假设:(1)设置的应变施加在样品上,(2)应力来源于样品自身的响应和(3)施加的流场为纯粹的剪切流场;之后具体阐述了这些假设失效的情形和所导致的常见的实验错误;最后,通过结合一些实验实例具体说明如何培养良好的测试习惯和获得可靠的测试结果.
关键词: 流变学 / 剪切流场 / 剪切流变测试
目录
1. 流场分类
2. 剪切旋转流变仪概述
2.1 测试原理
2.2 测试模式
3. 旋转流变仪测试中的常见问题
3.1 测试过程的基本假设和常见问题概述
3.1.1 输入(输出)应变为施加在样品上的应变
3.1.2 流场为简单的剪切流场
3.1.3 输入(输出)应力为样品的黏弹响应
3.2 测试中常见问题I:仪器和夹具柔量
3.3 测试中常见问题II:仪器和夹具惯量的影响
3.4 测试中常见问题III:样品自身惯量的影响
3.5 测试中常见问题IV:二次流的影响
3.5.1 同轴圆筒夹具二次流边界条件
3.5.2 锥板和平板夹具二次流边界条件
3.6 测试中常见问题V:样品表面张力
3.6.1 样品的各向对称性
3.6.2 样品本身表面张力大小
3.6.3 大分子聚集
3.7 测试中常见问题VI: 测试习惯
3.7.1 样品的制备:干燥和挥发问题
3.7.2 确定样品的热稳定性
3.7.3 样品体系是否达到平衡态
3.7.4 夹具热膨胀对测试的影响
3.7.5 夹具不平行和不同轴对测试的影响
4. 结论与展望
参考文献
流变学是研究材料形变和流动(连续形变)的科学,其重要性已在学术界和工业界得到了广泛的认可. 流变仪是研究材料流变性能的仪器,利用流变仪进行流变测试已成为食品、化妆品、涂料、高分子材料等行业的重要表征和研究手段[1~8].
本文从流变测试的角度,详细介绍了流场的分类和旋转流变仪测试的基本原理和测试技巧,重点阐述了剪切流变学测试中的基本假设和这些假设在特定的条件下失效的情况. 最后,通过结合具体的实验测试实例,详细地阐述了如何避免流变测试中的错误和不良测试习惯. 笔者希望本文能够对流变学测试人员有一定的帮助和启发,找到获得更可靠和准确的实验测试结果的有效途径.
1. 流场分类
高分子加工过程中的流场往往非常复杂,例如:在共混与挤出的工艺里,占主导的流场是剪切流场;在吹塑和纺丝等工艺里,占主导的流场是拉伸流场. 更多加工过程中,用到的流场是剪切与拉伸等流场的复合流场[9~12].
在流变学测试中,为了得到更明确的测试结果,往往选择比较单一和纯粹的流场,如剪切或者单轴拉伸流场(此后简称“拉伸流场”). 流变仪的设计往往需要实现特定的流场,并表征材料在该特定流场下的响应. 虽然剪切流场和拉伸流场在高分子加工中同等重要,高分子流变学的测试研究却呈现了一边倒的局面:目前大量常用的商用流变仪,如应力和应变控制型的旋转流变仪、转矩流变仪、毛细管流变仪的设计基础都是针对剪切流场的(利用这些仪器仅可进行比较粗略的拉伸流变测试,例如在旋转流变仪的基础上添加如Sentmanat Extensional Rheometer在内的附件测量拉伸黏度[13]或者利用毛细管流变仪的入口效应来估算拉伸黏度.),而针对拉伸流场的拉伸流变仪则比较稀缺.
剪切和拉伸流场自身的区别是造成以上局面的主要原因. 图1中分别展示了剪切和拉伸2种形变[14]. 施加剪切形变时(图1上),力位于样品顶部,力的方向与上表面平行,该应力会造成样品的剪切形变,而连续的剪切形变则称为剪切流动. 剪切流动的特点是,底部速度为0(不考虑滑移),顶部速度最大,速度梯度的方向与速度的方向垂直. 而施加拉伸形变时(图1下),力位于样品右侧,力的方向与右侧面垂直,该应力会造成样品拉伸形变. 同样,连续的拉伸形变称为拉伸流动. 拉伸流动的特点是,样品左侧固定,速度为0,右侧拉伸速度最大,因此速度梯度的方向与速度方向平行. 施加剪切流场时,剪切速率等于上表面的绝对速率除以两板间的距离. 在旋转流变仪中,使用匀速转动的锥板或者同轴圆筒即可实现单一的剪切流场. 然而,拉伸速率的大小等于右侧表面绝对速率除以样品的长度. 在拉伸过程中,样品越拉越长,因此右侧面的速度需要越来越大,方可实现稳定的拉伸流场. 假设t时刻样品的长度为L,则此时的拉伸速率等于[15]:
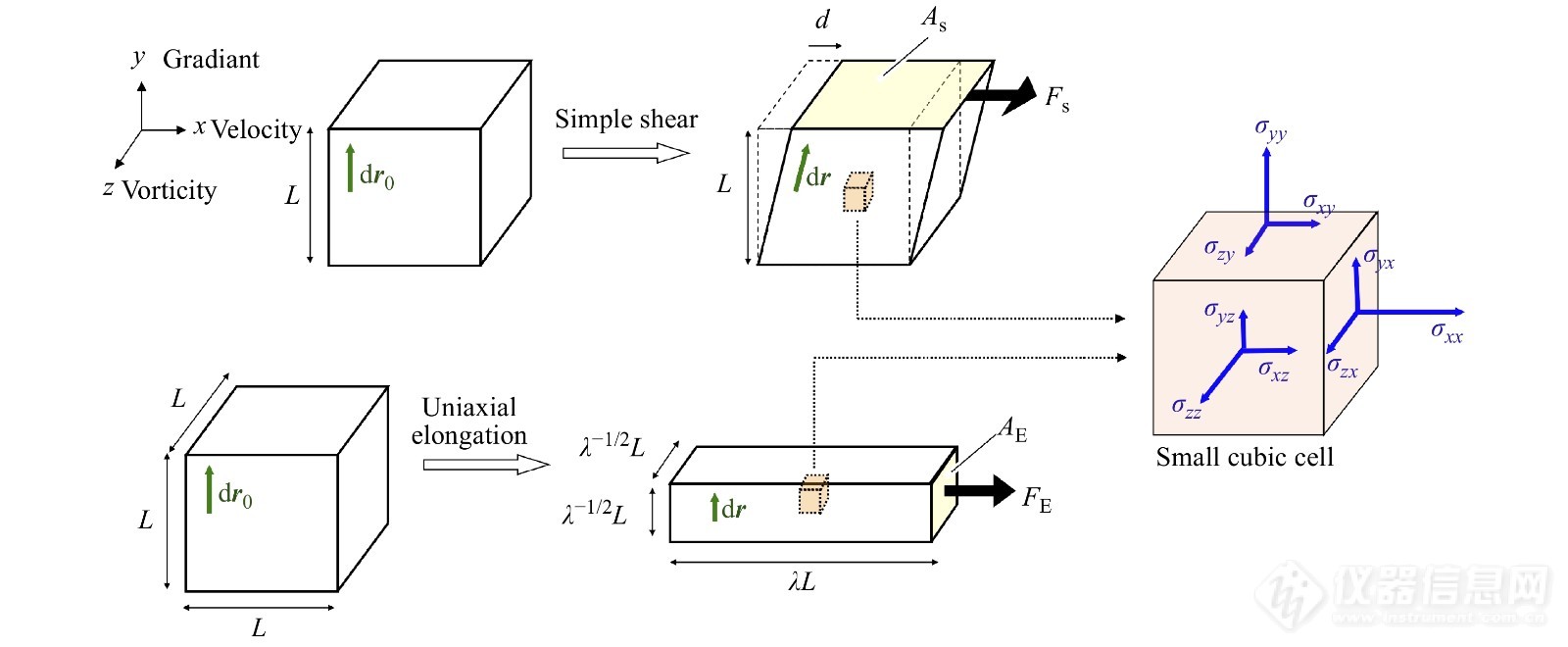
图 1
Figure 1. Illustration of two representative modes of deformation: the simple shear for which the direction of velocity gradient is perpendicular to that of velocity, and the uniaxial elongation for which the direction of velocity gradient is parallel to that of velocity. (Reprinted with permission from Ref.[14]; Copyright (2012) Elsevier)

将式(1)进行积分可以得到L(t)=L0exp(ε˙t),表明样品的长度正比于时间的幂律函数. 为了实现稳定的拉伸流场,实验中右侧面速度随时间呈指数增长,因此拉伸流场相较剪切流场更难以实现,这就是造成拉伸流变仪器较为稀缺的主要原因.
有人要问,为什么需要测试2种典型流场,我们能从剪切实验的结果来推导其拉伸的行为吗?对于线性流变的行为,答案是肯定的. 即当体系位于平衡态附近,施加微弱的扰动时,拉伸黏度ηE,0与剪切黏度η0存在着简单的正比关系ηE,0=3η0=3∫0tG(t′)dt′,其中G(t)为线性剪切模量相对于时间的函数[16,17]. 该正比关系由Trouton在牛顿流体中发现,被称作Trouton比[18]. 然而,对于流场较强的非线性的流变测试,无法从剪切流变行为直接推导拉伸流变行为,或反之,从拉伸流变行为推导剪切流变行为,主要原因是,剪切与拉伸测试不同流场下的应力张量的不同分量:如在图1中可见,剪切测试中主要测量上板作用力Fs,其除以上板面积可得到剪切条件下应力张量σ的xy分量,而拉伸测试中主要测量右侧力FE,其除以右侧面面积主要得到拉伸条件下应力张量的xx分量.
2. 剪切旋转流变仪概述
本文重点介绍剪切流变测试中的仪器原理和测试技巧(笔者计划在后续文章介绍拉伸测试的原理和技巧). 目前商业的用于剪切测试的流变仪为旋转流变仪和毛细管流变仪. 本小节主要围绕旋转流变仪展开介绍. 旋转流变仪主要分为应力控制型和应变控制型2种. 应力控制型旋转流变仪一般使用组合式马达传感器(combined motor transducer,CMT),即驱动马达和应力传感器集成在一端,也被简称为“单头”设计;应变控制型的流变仪一般使用分离的马达和传感器(separate motor transducer,SMT),即驱动马达和应力传感器分别集成在上下两端,简称为“双头”设计,这2种设计的主要区别在于:“单头”设计更为简单,仪器容易保养和维护,但是夹具和仪器的惯量、马达内部的摩擦力容易对应力的测试结果造成影响,需要对仪器定期进行校正;“双头”的设计更为复杂,仪器操作步骤较多,需要更专业的仪器培训和仪器维护来防止操作不当带来的仪器损害,但是由于其马达和应力传感器分离的优势,可以更准确地进行应变和应变速率控制模式的测量,“双头”的流变仪的测试范围更宽,可以在更高的频率和更低的扭矩下得到准确的测试结果.
下面我们将从旋转流变仪的测试原理(2.1节)和测试模式(2.2节)两个方面分别对于剪切流变测试进行简单的概述,这部分内容对于“单头”或者“双头”流变仪同样适用. 之后,我们会结合具体例子详细地介绍流变仪测试中需要注意的问题,部分内容会涉及“单头”和“双头”流变仪的区别. 对于流变测试比较熟悉的读者可以跳过2.1和2.2小节,直接阅读第3节.
2.1 测试原理
对于旋转流变仪,无论是应力控制还是应变控制模式,应变γ和应变速率γ˙均分别通过电机马达旋转的角位移θθ和角速率Ω转换得到,

而应力均通过扭矩T (T=R×F,其中F为力,R为力臂)转化得到,

上式中Kγ和Kσ分别为应变因子和应力因子,由测试夹具的类型、大小、间距等夹具的几何因子决定,而流变学测得的所有流变学参量,如剪切模量,黏度等都是应力应变的函数. 因此, 可以从原始测量的角位移θθ、角速率ΩΩ、扭矩T和应变因子Kγ、应力因子Kσ计算得到:

剪切流变测试中通常用到的夹具为平行板、锥板和同轴圆筒3种,其基本结构、流场特征,应变和应力因子(Kγ和Kσ)总结在图2中.
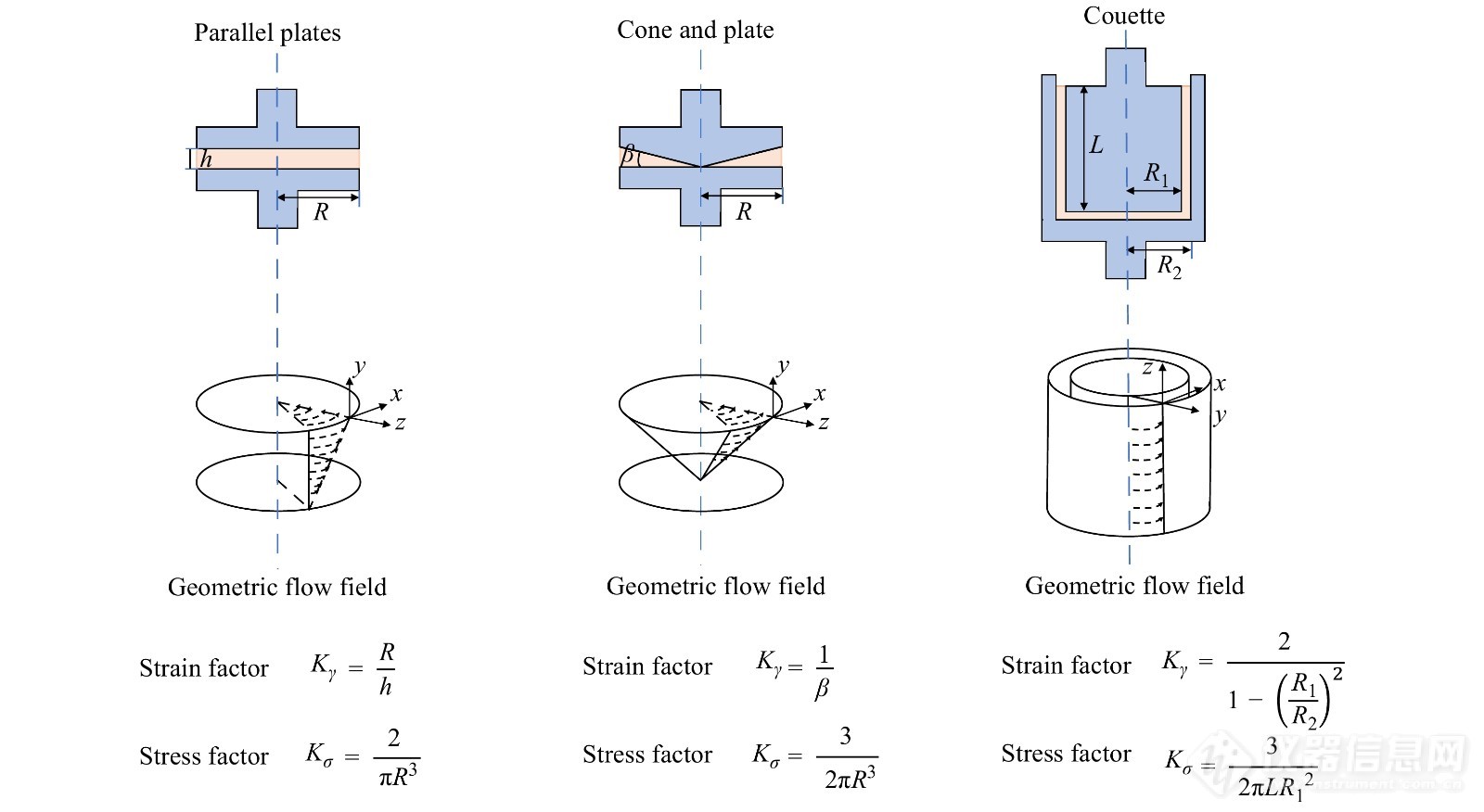
图 2
Figure 2. Geometry and parameters Kγ and Kσ of parallel-plate, cone-and-plate and Couette fixtures
平行板、锥板和同轴圆筒三者基本结构的特点也决定了其使用场合不同,具体总结如下:
(1)平行板夹具具有剪切流场分布不均一的特点,施加应变时,其圆心处剪切应变为0,最外侧剪切应变最大,应变沿半径方向线性增加;平行板夹具的优点是制样和上样都很方便,但由于其内部流场不均一的特点,平行板夹具一般只用于线性流变测试. 但是,对于一些特殊的实验需求,选择平板进行剪切实验具有一定的优越性. 例如,可以利用平板间剪切速率随半径线性增加的特性,研究不同剪切速率下的流动诱导结晶行为[19,20]. (2)锥板夹具相对于平行板夹具具有内部剪切流场均一的特性,但其制样和上样相对于平行板要复杂,特别是难以流动的样品上样比较困难,因此一般仅在非线性流变测试时选择. 此外,需要注意的是, 为了避免测试时锥板和其对面板直接接触,通常在锥面顶点处截去一小段锥尖,使用锥板测试时,设定的夹具间距即被截去的锥尖高度. (3)同轴圆筒夹具相对于平行板和锥板通常需要使用更多的样品,但是由于其具有较平行板和锥板更大的夹具/样品接触面积和测试力臂(介于样品内径R1和外径R2之间),使用其测试可得到更高的扭矩,因此,其可用于测试更低黏度的样品.
2.2 测试模式
仪器测试的基本原理通常是对样品施加一个扰动或者刺激并记录其响应. 在旋转流变仪的测试中,通常对样品施加应变并记录应力响应,或反之,施加应力并记录应变的响应. 根据施加应变或应力随着时间的变化情况,流变测试通常可以分为稳态、瞬态、动态3种测试模式(如图3),总结如下:
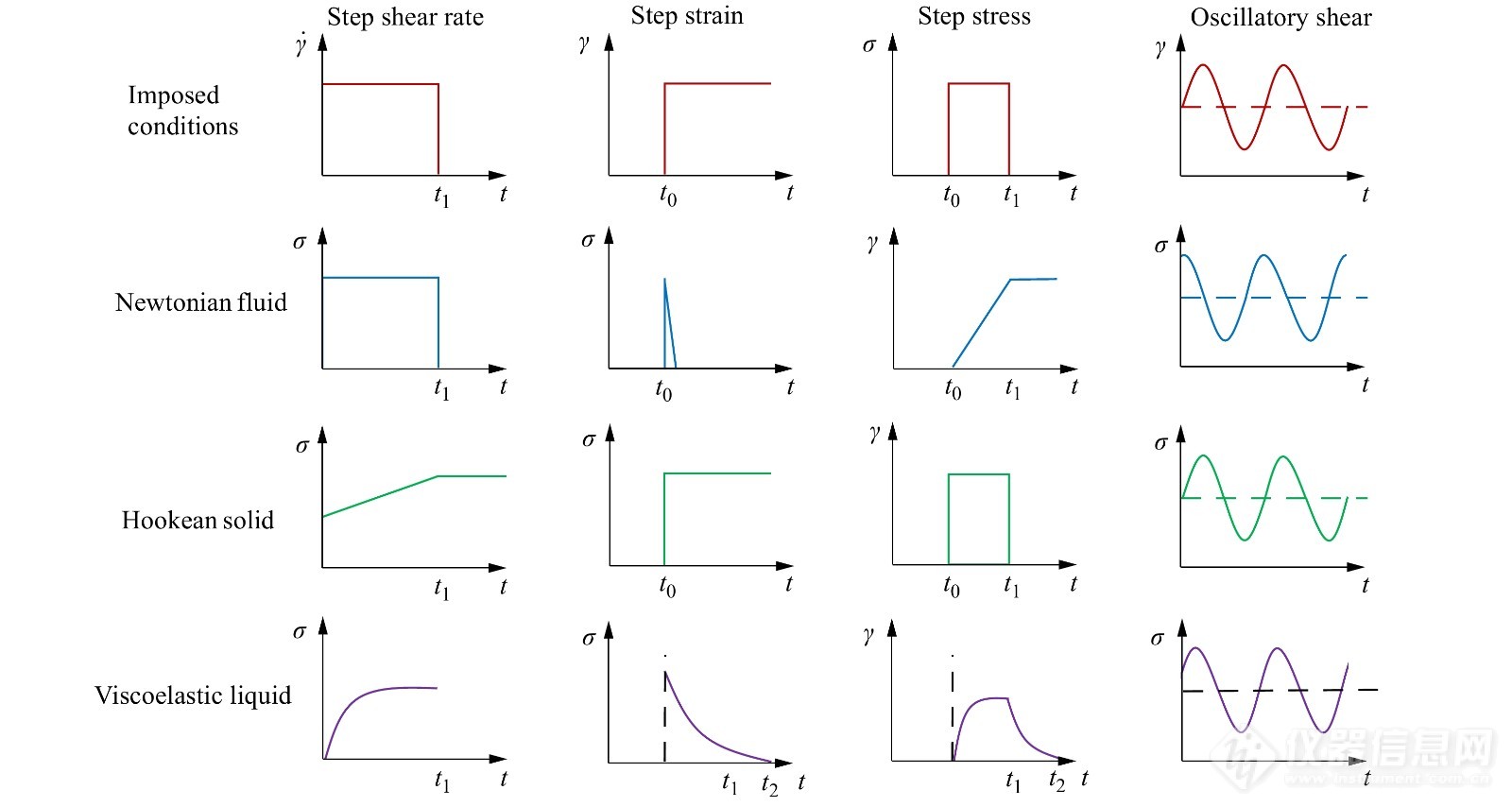
图 3
Figure 3. The different responses of Newtonian fluid, Hookean solid, and viscoelastic materials to the imposed steady flow (stress growth, transient or steady mode that depends on the focus), step strain (stress relaxation, transient mode), step stress (creep and recovery, transient mode) and small amplitude oscillatory shear (SAOS, dynamic mode).
(1)稳态测试模式通常测试样品在外加流场达到稳定状态下的响应. 通常,达到稳定的状态需要一定的时间,如果测试关注的是体系达到稳态过程,其测试模式一般称作瞬态模式,而如果测试关注的是体系达到稳态之后的过程,则测试模式为稳态模式. 通常仪器的软件内置了一些检验样品是否达到稳态的标准,如剪切速率扫描测试的过程中,仪器会记录应力的变化,当其测试应力在一定的时间内稳定后,仪器才会记录此时的应力. 剪切条件下,牛顿流体通常可以瞬间达到稳态流动,黏弹体通常需要一定的时间达到稳态流动,而胡克固体通常应力随应变增加,在结构不破坏的前提下无法达到稳态流动. (2)瞬态测试模式通常指从一个状态瞬间变化到另一个状态的过程,如施加阶跃应变(应变控制模式)、阶跃应力(应力控制模式)或者阶跃剪切速率等. 其中最典型的测试就是,施加一个固定应变,记录应力随时间变化的应力松弛(stress relaxation)测试,施加或撤销一个固定的应力,记录应变随时间变化的蠕变和回复(creep and recovery)测试,或者施加一个阶跃剪切速率,记录瞬态黏度随时间变化的应力增长测试(stress growth). 这些测试的共性是关注样品在一个特定刺激下的转变过程. 以阶跃应变为例,迅速施加应变后,牛顿流体的应力可迅速松弛,胡克固体的应力达到一个恒定值无法松弛,而黏弹体的应力需要经过一定的时间松弛,这个时间通常反映黏弹体系在应变下结构重整的特征时间. (3)动态测试模式是施加一个交变的应变或者应力,如正弦变化的交变应变或者应力,并记录响应. 以施加正弦应变的测试为例,由于测试的频率和应变大小均可调整,因此,测试有很大的参数空间. 通常,小应变下,体系结构仅稍微偏离无扰状态,应力响应的信号也是正弦波,该测试通常被称作小振幅振荡剪切(small amplitude oscillatory shear,简称SAOS). 对于胡克固体,应力的相位与应变相位相同;而对于牛顿流体,则应力的相位与应变速率(应变对时间的导数)的相位相同,与应变相位差π/2;对于黏弹体,应力的相位与应变的相位在0~π/2之间. 当应变较大时,体系的结构严重偏离无扰状态且随时间改变,此时的应力响应通常不是正弦波,该测试通常被称作大振幅振荡剪切(large amplitude oscillatory shear,简称LAOS). 需要指出的是,一些仪器软件会用正弦波来拟合非正弦的应力结果得到包括模量在内的测量结果,此时对于结果的解读需要非常小心. 因此,一般的测试过程中建议打开仪器的应力记录来观察测量应力波的波形,并据此判定测试的线性/非线性.
3. 旋转流变仪测试中的常见问题
3.1 测试过程的基本假设和常见问题概述
上文提到,旋转流变仪的原始测量的角位移θ和扭矩T可转化为应变和应力. 然而,测量的应变和应力是否就是施加在样品上的真实的应变和应力呢?这显然是流变测试中最关键的问题. 需要指出的是,旋转流变仪的测试结果是建立在3个基本假设上面的:(1) 应变作用在样品上;(2) 应力为样品自身的响应;(3) 流场为简单剪切流场. 这些假设都是会在一定的测试条件下失效,从而导致测试结果不可靠. 接下来我们将详细地介绍这些假设条件分别在什么测试情况下失效.
3.1.1 输入(输出)应变为施加在样品上的应变
该假设的关键在于没有考虑仪器和夹具柔量的影响,即假设样品的应变可以直接从角位移得到. 然而,在力的作用下,仪器和夹具自身也会旋转一定的角度. 只有当该角位移远小于作用在样品上角位移时,上述假设才能成立.
由于夹具通常由不锈钢或者其他金属材料制造,其模量通常在~1011 Pa或者更高的范围,而测试样品,特别是高分子材料即使是在玻璃态,模量通常小于1010 Pa,因此,似乎夹具的形变可以忽略. 但是,需要指出的是,平板和锥板的夹具通常被设计成细长空心的圆柱形,而夹具中间的样品通常为扁平的圆片状,这种形状上的差异会显著增加夹具柔量的影响.
除此之外,夹具与样品之间的滑移也可造成施加应变和样品实际应变的区别[21~23]. 这种滑移会消耗一部分施加的角位移,假设被消耗的角位移为θslip,则样品上的实际角位移θeff小于施加的角位移θ(=θslip+θeff). 对于平行板样品,由于应变参数Kγ=R/H,这使得在相同的实际应变Kγθeff下,旋转的角位移θeff随着板间距H的增加而增加,而θslip则改变较少,因此,滑移的效应会随着板间距的增加而弱化,该结果也可以用做滑移是否存在的间接判据:即如果存在滑移,则其造成的误差会随着板间距的增加而减少. 对于滑移效应更为直接的判据就是通过微小的示踪粒子直接观测板附近的粒子的运动是否和板的运动一致.
3.1.2 流场为简单的剪切流场
上文中提到,剪切流变仪设计的一个基本原则就是生成纯粹的剪切流场并记录样品在该流场下的响应. 然而,由于受到界面和样品自身的影响,样品中实际的流场未必为纯粹的剪切流场,该效应通常在大剪切速率下出现. 例如,对于同轴圆筒夹具测试低黏度样品,当泰勒数大于一个定值时,或者对于平行板和锥板测试低黏度样品,当雷诺数大于一个定值时,流场会偏离简单的剪切流场. 以平行板为例(如图4所示),在高雷诺数下,由于离心作用,旋转的上板附近的流体沿着板的径向向外运动,为了填补这些流体流出的空隙,静止下板附近的流体会沿着径向向内运动,这2种流体的运动就会造成一次流基础上出现叠加的二次流,从而导致测试扭矩的增加和相应的剪切增稠假象[24].
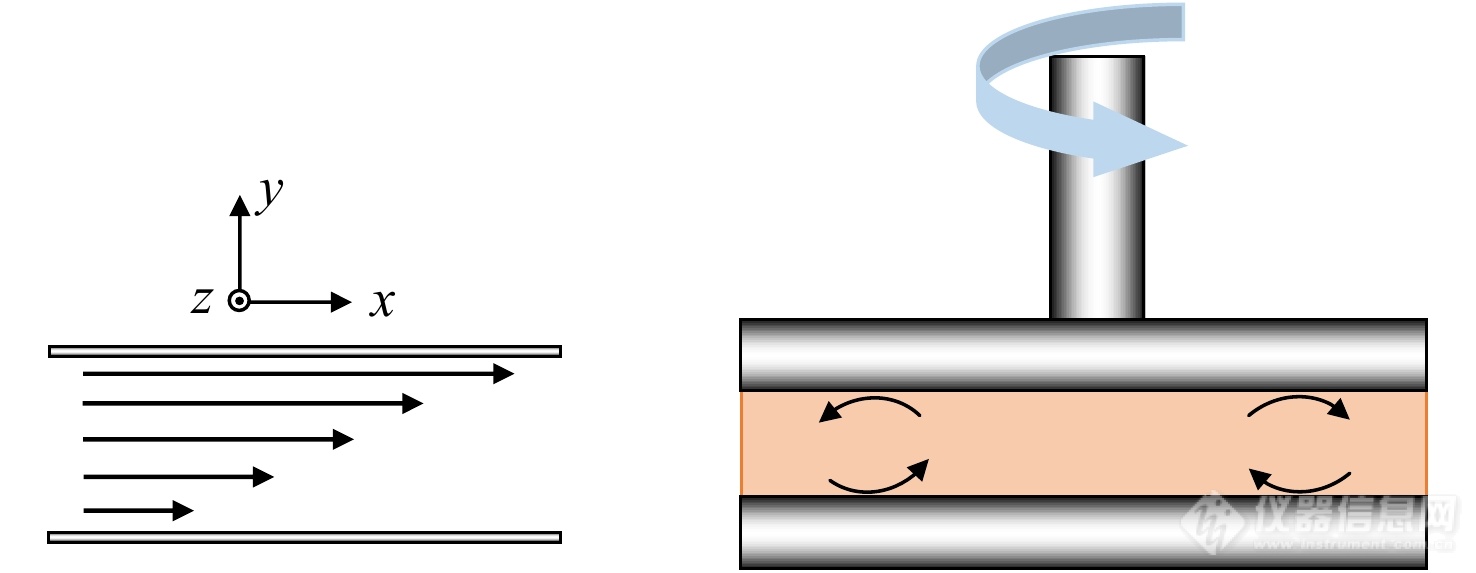
图 4
Figure 4. The secondary flow occurs when sample under rotary geometry moves radially outward and sample on the static geometry moves radially inward.
对于具有一定弹性的样品,假设其自身的松弛时间为τ,当韦森堡数Wi = τγ˙大于1时,也可能会在低泰勒数(同轴圆筒)或者低雷诺数(平行板或者锥板)的条件下出现弹性非稳定二次流,这种二次流的出现也会造成剪切增稠的假象. 下文中,我们会对同轴圆筒和锥板以及平板出现二次流的边界条件进行更详细的讨论.
此外,在高度缠结的高分子溶液或者高分子熔体等黏度较高的体系中,剪切速率过高的时候可能会出现剪切带或者较强的壁面滑移,这种剪切速率的非均一分布往往有利于体系自由能的降低. 对于高分子熔体,在高剪切速率时,自由表面附近可能出现熔体破裂的现象. 这些现象的出现也都会导致测量体系的流场严重偏离简单剪切流场.
通常,剪切带、壁面滑移和熔体破裂等现象都会导致体系的应力减少及随之增强的剪切变稀效应(应力或者黏度随时间急剧下降). 对于一些极端的情况,甚至会出现剪切应力σ不随剪切速率γ˙γ˙的增加而增加的特殊现象(此时黏度η = σ/γ˙γ˙~γ˙β且β≤−1).
为了减弱熔体破裂的现象带来的实验误差,通常可以采用锥板加组合板的特殊夹具(cone- partitioned plate,简称CPP夹具)(如图5所示). CPP夹具中,锥板(绿色)与马达相连,组合板分为2个部分,中心平板(尺寸小于锥板,灰色)和环绕中心平板的环状板(蓝色),两者同轴且分离,共同组合成类似于与锥板同等大小的平板. 其中,中心板与传感器相连并记录扭矩,环状板与仪器相连且被固定. 测试过程中,一般熔体破裂发生在样品边缘. 因此,只要当破裂的边缘没有深入到中心板,所记录的扭矩受到边界熔体破裂的影响就可以忽略[25].
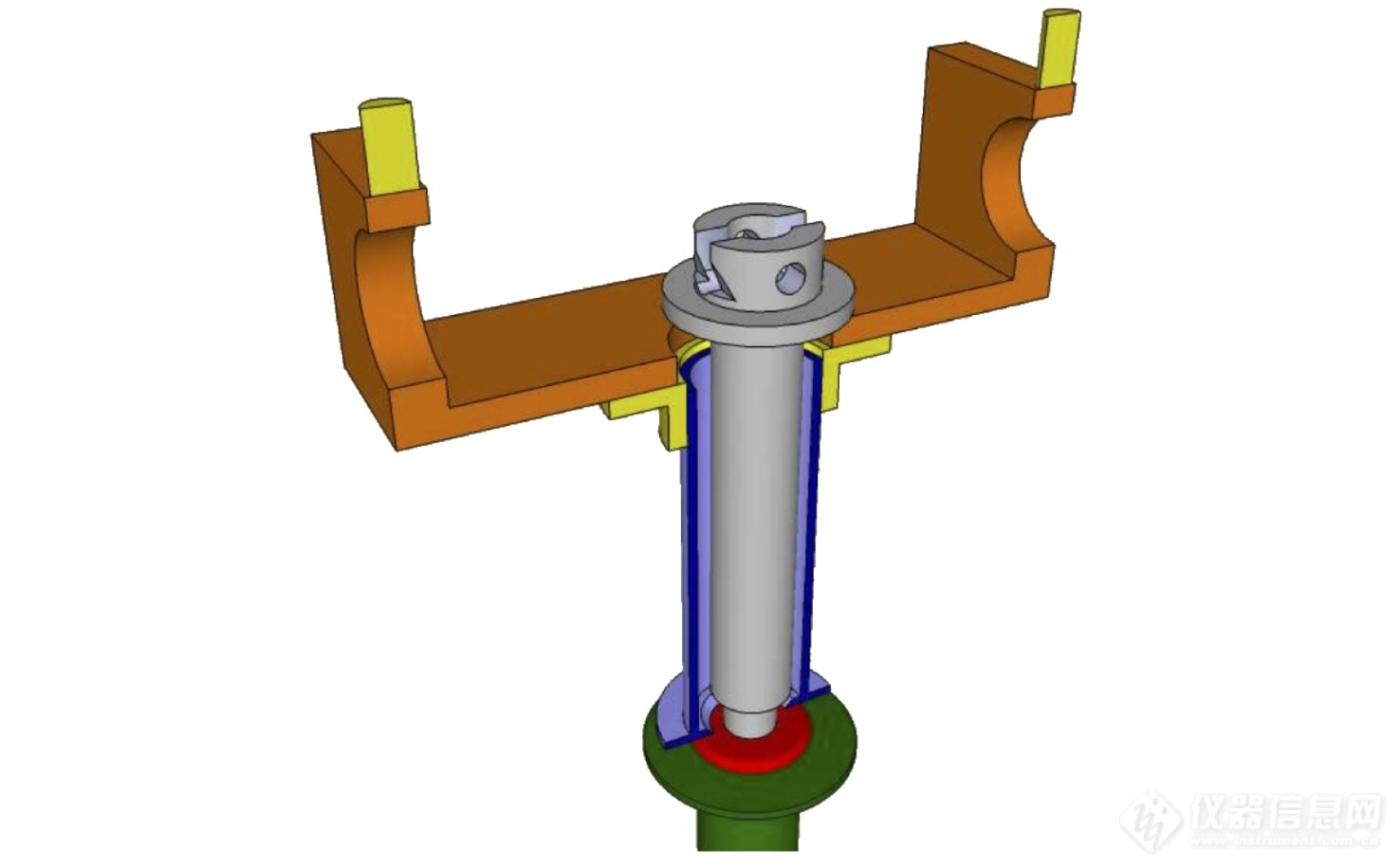
图 5
Figure 5. Schematic view of the CPP fixture. Green: cone; red: sample; blue: outer partition (section); yellow: translation stages (section); orange: bridge (section); grey: inner tool (Drawing not in scale). The sample disk should have size sufficiently larger than the inner plate. (Reprinted with permission from Ref.[25]; Copyright (2016) American Chemical Society)
3.1.3 输入(输出)应力为样品的黏弹响应
其实,上述二次流出现是由样品内部流场的不稳定性带来的效应,会导致额外的应力. 在流变测试中,另一个无法忽略的就是测试扭矩的贡献中包含仪器和夹具自身的惯量的贡献. 对于真实样品的测试扭矩应该等于测试总扭矩减去仪器和夹具自身的惯量造成的额外扭矩.
上面文中提到,对于纯弹性的流体,流变测试中其自身的弹性产生的扭矩T与旋转角度θ具有正比的关系,即T~θ,此时T相对于θ的相位角δ为0°;对于纯黏性的样品,流变测试中其自身的黏性所产生的扭矩与旋转角度相对于时间的导数具有正比的关系,即T~θ˙,此时T相对于θ的相位角δ为90°;对于惯性导致的扭矩,其大小与加速度成正比,即T~θ¨,此时T相对于θ的相位角δ为180°,这种区别可以作为出现惯量效应的判据. 例如,在动态测试中,样品黏弹性引起的相位角在0°和90°之间,一旦测试时出现了90°和180°之间的相位角,则必然出现了仪器惯量效应. 特别是在高频动态测试中,由于θ = θ0sin(ωt),则惯量I贡献的扭矩高达T0 = Iω2θ0,因此,商业的旋转流变仪通常频率ω的测试上限在102 rad/s. 虽然有些仪器支持测试更高的频率,如103 rad/s或者更高,但是测试高于102 rad/s的数据时,需要时刻注意分析惯量对于扭矩的贡献.
此外,由于自由表面的存在,表面张力对于扭矩的贡献有时也是难以忽略的,该贡献在低黏度的样品中表现得尤为突出. 由于表面张力的存在,样品具有收缩表面积的趋势,这会造成剪切作用下界面形状或面积变化时额外的法向力或者剪切力. 例如,在平板和锥板夹具中,样品过度充满或者未充满的时候,样品的自由表面会产生突出或者凹陷的曲面结构,这种曲面结构的产生会引起额外的法向力. 当样品在剪切流场中,自由表面的面积也会随之出现波动性的变化,这种变化通常会产生弹性应力响应,从而导致额外的应力贡献. 通常可以通过填充合适量的样品、增加样品的各方向对称性和引入表面活性剂降低表面张力等方法来抑制表面张力的影响.
下文中,我们会结合一些实验实例进一步阐释上述旋转流变仪测试的假设条件失效的情况. 此外,我们总结了流变测试中一些不良测试习惯导致无法正确获取实验数据的情况. 最后,我们会针对上述内容,给出一些避免类似错误结果的建议.
3.2 测试中常见问题I:仪器和夹具柔量
流变仪能够准确测量样品模量的一个前提是传感器和夹具的柔量远小于样品的柔量,或者换言之,传感器和夹具的刚度远大于样品的刚度(刚度等于柔量的倒数). 其中,夹具的刚度不仅与夹具的模量相关,也与夹具的尺寸和形状相关. 如果将夹具设计成圆柱形,则其刚度κ与夹具横截面半径R的4次方成正比,与圆柱体的高h成反比:

一方面,为了抑制样品的温度对传感器和马达的影响,并减少夹具的惯量,平行板和锥板夹具常被设计成细长的形状(较小的R和较大的h),这种结构会减少夹具的刚度;另一方面,为了增加样品的测试扭矩,常将样品制成扁平的形状,这种形状的差别使得夹具与样品刚度的区别远低于制造夹具的材料和样品模量上的区别,而导致实际施加在样品上的真实应变低于设定应变,这种应变的误差会导致样品流变测试结果的显著误差. 例如,刘琛阳等分析了双头应变控制型流变仪ARES G2(TA)的仪器柔量对线性黏弹性的影响[26]. 如图6(a)所示,在样品模量大于105 Pa时,用25 mm平行板的测量结果明显偏离8 mm平行板的测量结果. 虽然样品的模量不发生变化,样品的刚度随着尺寸R的增加而增加,造成了测量时夹具产生了更多的形变,这导致了实际施加在样品上的应变的减少和相应的测试模量的降低;为了说明这个问题,图6(b)展示了相对于指令应变(黑色方块),经过传感器校正后的实测应变(红色圆点)较小,而经过夹具校正后的应变则更小(绿色三角),该应变可反映施加在样品的实际应变.
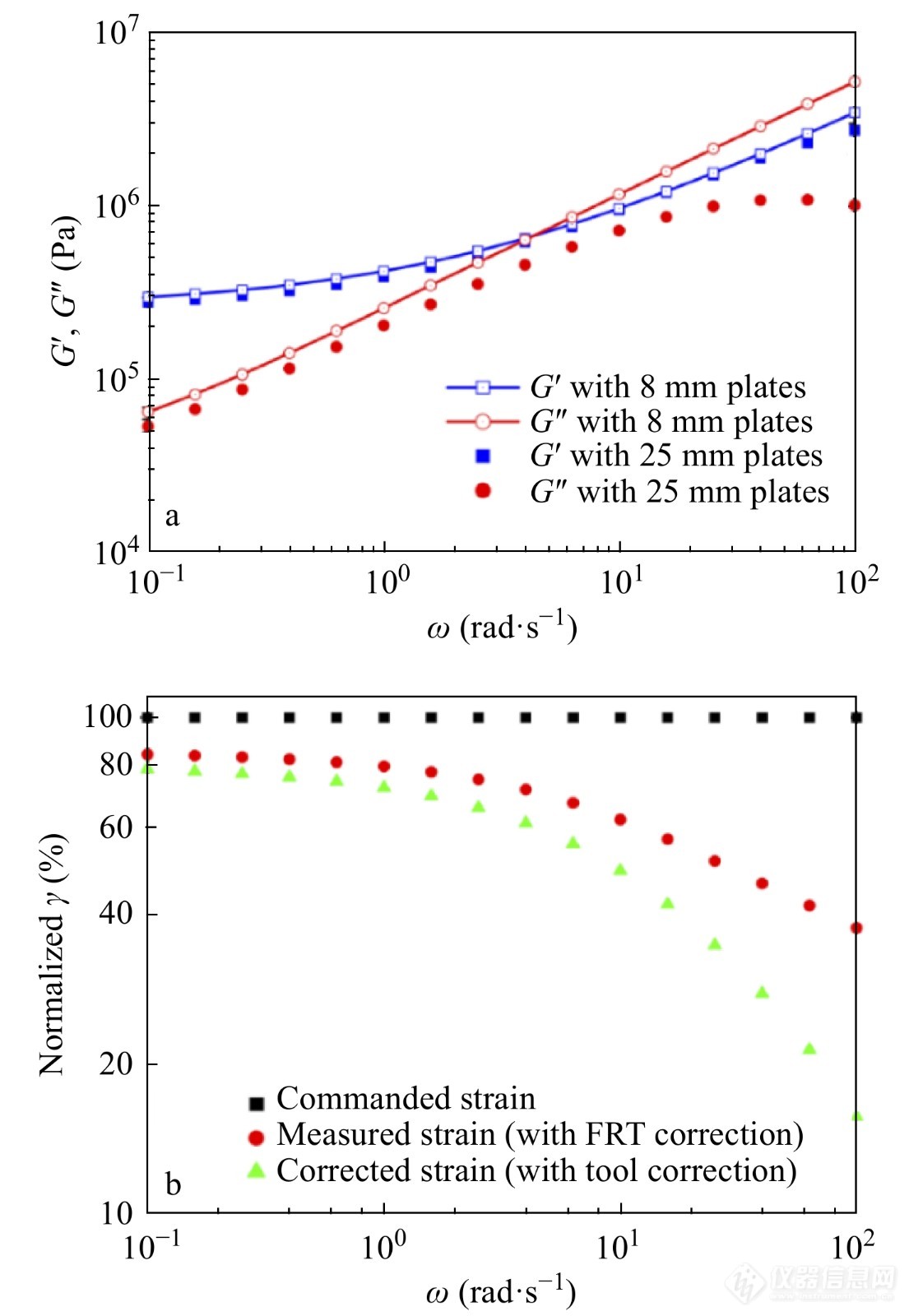
图 6
Figure 6. (a) The effect of geometry compliance on linear viscoelasticity; (b) Comparison of commanded strain (as 100%), measured strain (with force rebalance torque transducers (FRT) compliance correction), and corrected strain (with tool correction) obtained for a polyisobutylene sample at −20 °C using 25 mm parallel plates (Reprinted with permission from Ref.[26]; Copyright (2011) Society of Rheology)
为了准确地测量样品的模量,通常建议选取合适尺寸的夹具来直接测量. 由于夹具的形变通常正比于扭矩,因此在测量较高模量范围的样品时,为避免柔量的影响,需减少样品和夹具尺寸来降低扭矩. 而对于测量较低黏度的样品,需要增加样品和夹具的尺寸来增加扭矩,使得扭矩大于仪器传感器的测试下限. 笔者的经验是,25 mm板使用的上限通常为~105 Pa,8 mm板的使用上限为~107 Pa,而如果需要准确地测量高分子玻璃态模量(~109 Pa),需要使用3 mm左右的夹具. 对于黏度极低的样品,除了选择更大的板(如50或60 mm的夹具)以外,还可以使用过采样技术(oversampling)[27],拓宽动态测试的扭矩测试下限,提高相位角的准确程度.
但是考虑到小夹具上样的困难,可利用柔量校正来拓展夹具的使用上限. 很多流变学者具体研究了柔量的校正方法,例如1982年,Gottlieb和Macosko[28]讨论了仪器柔量对动态流变测量的影响以及力传感器的校正方法. 在2008年,Hutcheson和McKenna[29]详细地研究了夹具尺寸对玻璃化转变区附近的流体的动态振荡测试和应力松弛测试结果的影响,并提出相应的校正方法.
本文以Hutcheson 和McKenna的校正方法为例[29],简单介绍一下动态剪切数据的校正方法. 为了准确测定特定夹具下整个仪器系统的柔量系数,作者设计加工了上下板“连体”的参比夹具(如图7所示),并直接测量了参比夹具的柔量. 根据柔量相加原则,流变仪器实测复合扭转刚度κ0∗的倒数等于仪器夹具刚度κt和样品刚度κs∗的倒数之和:

由于仪器和夹具的柔量均来源于其固体弹性,可以将两者简化为一个与黏弹样品串联的弹簧,其刚度可简化为实数κt. 在已知κt的基础上,可利用公式(6)校正测试的实验数据κmes∗,得到样品的实际复数刚度κs∗.
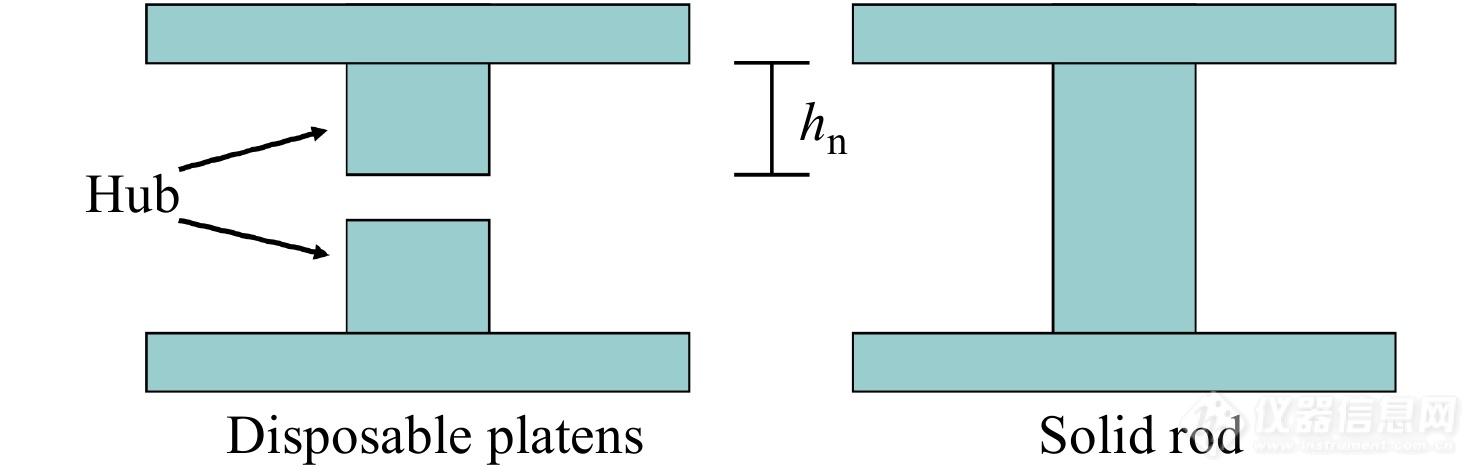
图 7
Figure 7. A simple schematic showing the geometry of the solid rod and the disposable platens (Reprinted with permission from Ref.[29]; Copyright (2008) American Institute of Physics).
3.3 测试中常见问题II:仪器和夹具惯量的影响
对于仪器和夹具惯量的校正是准确进行瞬态和动态流变测试的基础. 旋转流变仪测得的扭矩不仅来源于样品自身的应力响应,也来源于马达和夹具在加速过程中的惯量贡献. 早在1991年,Krieger等讨论了单头的应力控制型流变仪仪器和夹具惯量对测试的影响[30],他们发现,当仪器施加恒定的扭矩时,部分扭矩用于加速驱动马达和夹具旋转,当旋转速度达到稳定时候,测试的扭矩才是真实的样品扭矩. 最近,Lauger等研究了流体在振荡剪切模式下的仪器和夹具惯量的影响[31],并给出了通过流变仪测量的实测扭矩、样品产生的扭矩以及仪器和夹具自身惯量产生的扭矩的三者之间的矢量关系(图8).
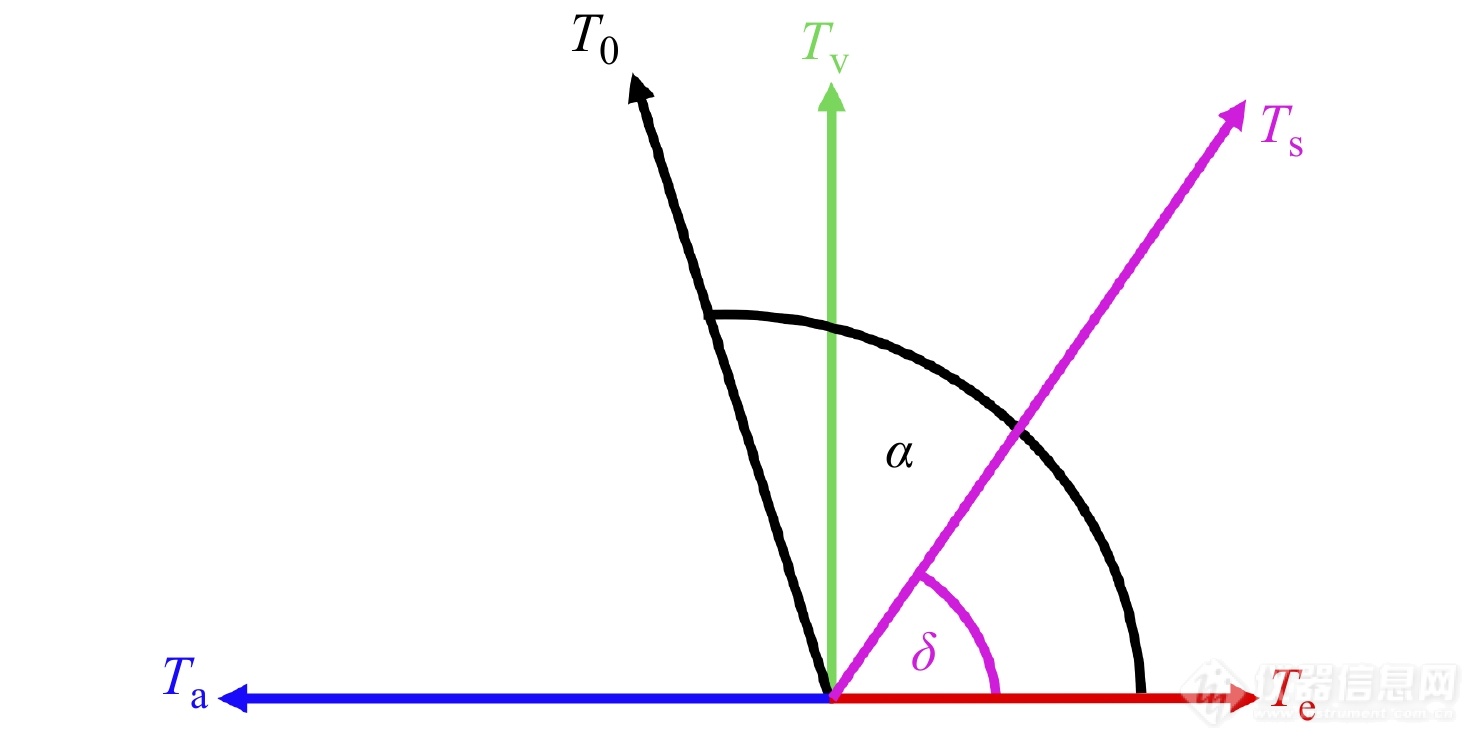
图 8
Figure 8. Vector diagram of torques, including acceleration torque Ta, total or electrical torque T0, and sample torque Ts, where δδ and αα are phase angle of T0 and Ts, respectively. The sample torque can be decomposed into viscous part Tv and elastic part Te (Reprinted with permission from Ref.[31]; Copyright (2016) Society of Rheology).

其中,仪器测试的实测扭矩T0等于样品扭矩Ts和仪器加速惯量产生的扭矩Ta之和. 换言之,样品产生的扭矩应该等于总扭矩减去仪器加速时惯量产生的扭矩,该扭矩可利用相位角分解成弹性贡献部分Te和黏性贡献部分Tv.
此外,Lauger等研究表明[31].:对于牛顿流体,惯量产生的扭矩与样品扭矩的比率可表达为

其中I为测量设备的转动惯量,|G∗|为样品的复数模量的绝对值,ω为测试的角频率. 然而,需要指出的是公式(8)仅适用于牛顿流体,对于黏弹性体系并不准确.
据此,可以通过计算仪器和夹具惯量产生的扭矩与样品扭矩之比来判断仪器和夹具惯量的影响. 例如:图9展示了Lauger等利用单头的MCR系列流变仪(Anton Paar)测试黏度为4 mPa·s的S4 oil频率扫描测试. 在测试的频率范围内,该流体应为牛顿流体. 其中蓝色正三角表示实测的扭矩T0,绿色倒三角表示校正了仪器和夹具惯量贡献后的样品贡献的扭矩Ts. 在最低频区域,实测扭矩与样品贡献扭矩近似相等,说明样品的贡献占主导,此时测得的复数黏度(红色圆)接近样品稳态黏度4 mPa·s. 但是随着频率的增加,实测扭矩大于样品贡献的扭矩且两者差距逐渐增加,在频率小于25 rad·s−1(竖箭头所示)的区域,虽然实测扭矩已经远大于样品的扭矩贡献,即实测的T0/Ts已接近2个数量级(横箭头所示,这与通过公式(8)计算的结果Ta/Ts=Iω2Kσ/(Kγ|G∗|)=IωKσ/(Kγ|η∗|)= 95近似相等),经过校正得到的样品扭矩计算的黏度仍然接近4 mPa·s,说明测试结果仍然有效. 该例子展示了当前流变仪的技术水平已经臻于成熟:即使在惯量贡献的扭矩占主导的情况下,仍然可以通过仪器校正得到准确的样品扭矩. 但是在频率高于25 rad·s−1区域惯量校正开始失效,造成了稳态黏度激增的假象.
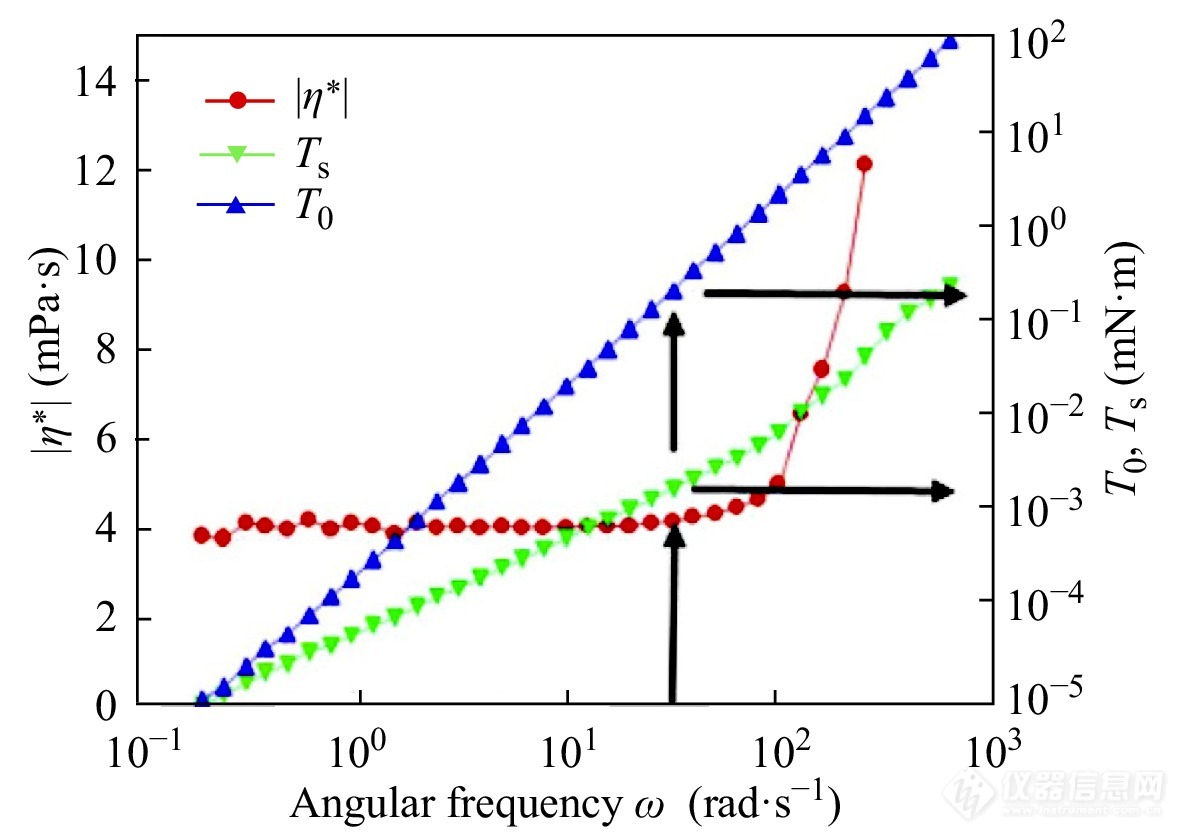
图 9
Figure 9. Frequency sweep measurement on the S4 oil sample with viscosity of 4 mPa·s (CP60-0.5 geometry). In addition to the complex viscosity, the measured total torque T0 and the sample torque Ts obtained after the inertia correction are plotted against angular frequency ωω. Arrows point to data points at 25 rad·s−1 (see text), above which the inertia correction fails. (Reprinted with permission from Ref.[31]; Copyright (2016) Society of Rheology)
在动态振荡测试中,样品黏弹性引起的相位角应当在0°和90°之间(图8所示),因为90°和0°相位角分别对应纯黏性和纯弹性的扭矩贡献Tv和Te,而惯量产生的相位角为180°. 图8中,高频处仪器测试的实测扭矩T0远大于样品测试扭矩Ts,表明仪器加速扭矩Ta在测试T0中占据主导,此时的相位角应接近180°. 因此,一旦测试时出现了90°和180°之间的相位角,或者动态测试出现G'~G"~ω2的结果,即可判定出现了仪器惯量效应[32]. 为了避免实验测试中的不良数据,仪器惯量造成的扭矩Ta与材料自身产生的扭矩Ts之比Ta/Ts应小于一个极限值(该值与仪器的状态和校正的准确性相关).
减少惯量影响的一个行之有效的方法是选择合适的夹具. 公式(8)中,与夹具几何尺寸相关的参数为Kσ/KγKσ/Kγ. 对于锥板,Kσ/Kγ=3β/(2πR3),因此, 减少锥角ββ和增加板半径R均有利于减少惯量影响,而对于平板,Kσ/Kγ=2h/(πR4),因此,减少板间距h和增加板半径R均有利于减少惯量影响,或者选择更轻质的夹具来减少I亦可减少惯量影响. 总之,无论锥板或平板,增加R或者选择轻质夹具都是减少惯量影响的有效手段.
为了降低仪器和夹具惯量影响,对于单头的应力控制型流变仪,需要定期进行惯量的校正,并在更换夹具时做相应的校正. 对于双头的应变控制型的流变仪,使用具有力反向平衡功能的传感器可以极大地抑制惯量带来的误差,其表现虽远超单头的流变仪,但也无法完全消除惯量的影响. 因此,需要对具体的实验测试结果进行综合的分析和甄别.
3.4 测试中常见问题III:样品自身惯量的影响
剪切流变仪测试中一个基本假设是流场的单一性,即流场是纯粹的剪切流场,这一假设在高速振荡测试过程中失效[33]. 即在振荡测试中,流变仪通过夹具迫使样品产生往复运动,使得样品内部产生剪切波,当板(夹具)间距与剪切波波长相当或大于剪切波波长时,样品的自身惯量的影响会使得施加样品的剪切流场偏离纯粹的剪切流场.
Schrag给出了在剪切流变测试不受该剪切波干扰的临界条件[34],即板间距需远小于其波长λs,其表达式为:

式中ρ是流体的密度,|η∗|=|G∗|/ω是复数黏度的绝对值,其中|G∗|是复数模量的绝对值,δ是相位角. 研究表明,在给定的频率范围内选取合理的板间距h是减少样品惯量影响数据误差的关键. 以水为例,密度为ρ≈1 g·cm−3,黏度为η≈10−3 Pa·s,相位角δ≈90°,当频率ω=102 rad·s−1时,可估算出λs≈0.9 mm. 用平板测试一般要求间距在0.5~1 mm,因此无法满足h<<λs. 当使用锥板测试时,板间距最宽的部分可以估算为h=βR,因此,半径为25 mm、锥角为1°的锥板,h=0.44 mm,同样也无法满足h<<λs. 由公式(9)可知剪切波长λs随着样品黏度的增加而增加,因此,上述问题一般不会在黏度较高的高分子溶液或高分子熔体中出现.
图10展示了Lauger等利用双头的MCR系列流变仪(Anton Paar)对牛顿流体S4 oil 在半径相同(R=30 mm),锥角分别为0.5°(红色)、1°(绿色)、2°(蓝色)不同的夹具下的振荡剪切测试,研究了样品惯量对流体相位角的影响[31]. 该流体在测试范围内为牛顿流体. 我们发现样品在低频区域表现牛顿流体性质,相位角均为90°,随着频率的增加,相位角逐渐降低,流体出现了一定的弹性响应,且锥角越大,相位角降低越多(箭头指向). 相位角的减少导致了储能模量G'~ω2的标度区域的出现,该结果非常类似于黏弹流体的松弛末端行为,但其实为样品惯量造成的实验假象. 显然,此相位角减少的不同来源于测试夹具的区别而非样品的区别. 究其原因,是锥板最外侧的板间距βR (0.5°, 1°, 2°板分别为0.26,0.52和1.05 mm)逐渐逼近于通过公式(9)计算出来的λs≈2.0 mm,使得样品惯量造成的实验误差逐渐显现.
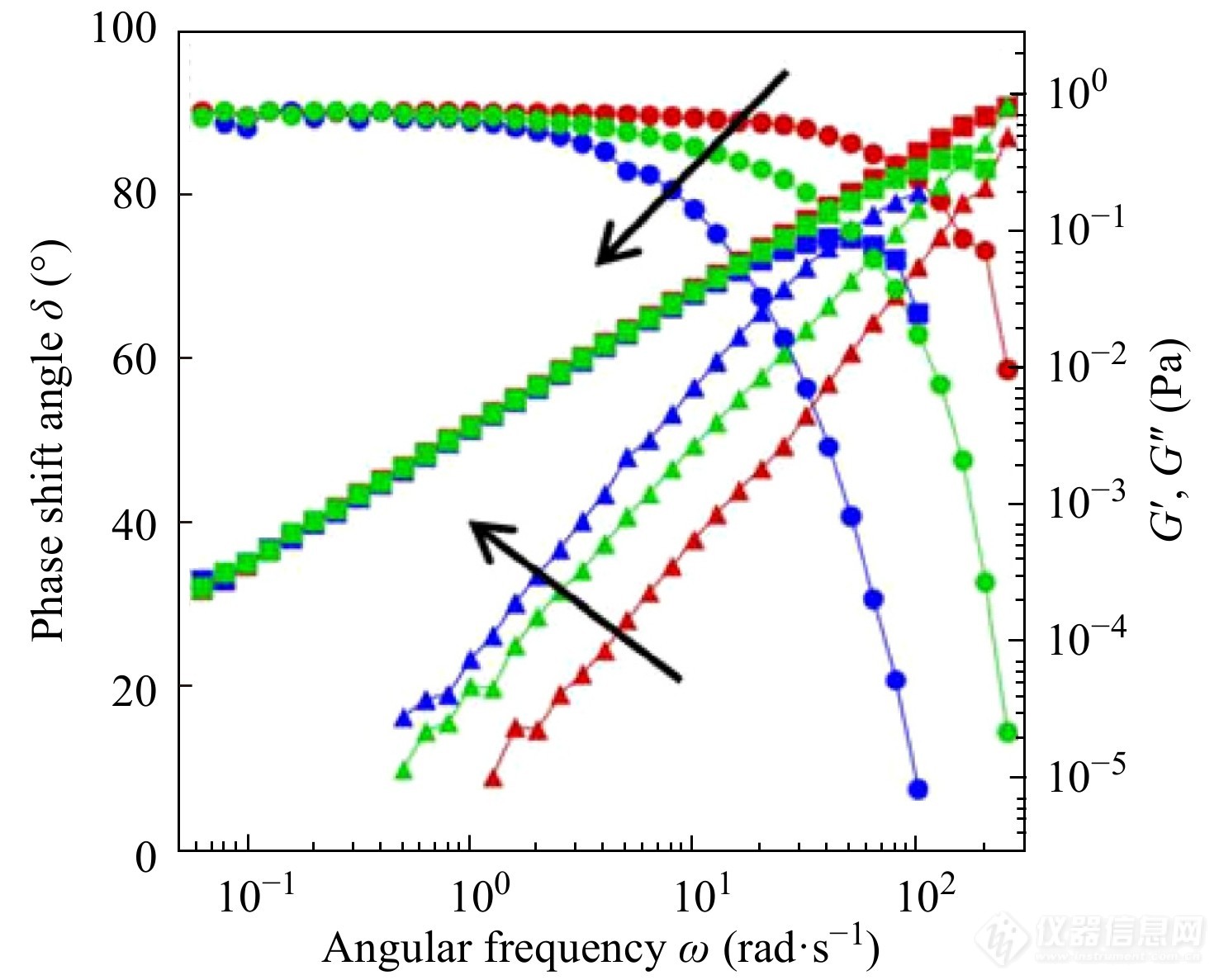
图 10
Figure 10. Phase angle (circles) and storage G' (triangles) and loss modulus G" (squares) for the S4 oil measured in SMT mode with three cone angles, 0.5° (red), 1° (green), 2° (blue). The arrow indicates the direction of increasing the cone angle. (Reprinted with permission from Ref.[31]; Copyright (2016) Society of Rheology)
3.5 测试中常见问题IV:二次流的影响
在稳态或瞬态测试中,高剪切速率时,由于流动不稳定性的影响可能导致剪切流场出现失稳,造成二次流的出现[24,35~37],使得剪切流变仪测试中剪切流场单一性的基本假设失效. 二次流叠加在剪切流场上,会增加仪器测量的扭矩,导致测试样品的表观黏度突然增加. 研究表明,对于不同夹具,均可出现二次流. 下面我们将对同轴圆筒、锥板和平板3种夹具的几何流场出现二次流的边界条件进行阐述,并通过实例展示二次流对实验数据的影响.
3.5.1 同轴圆筒夹具二次流边界条件
泰勒给出了牛顿流体在同轴圆筒夹具的测量过程中失稳的临界条件[38~40]:可避免Taylor-Couette涡流出现的稳定区间的泰勒数Ta满足:

其中R1和R2分别为同轴圆筒夹具中流体的内径和外径(如图2所示),而同轴圆筒夹具的剪切速率为:γ= ΩKγ≈ ΩR1/(R2 − R1),由此可以得到避免Taylor流的条件:

3.5.2 锥板和平板夹具二次流边界条件
锥板和平板具有不同于同轴圆筒的边界条件,其产生二次流的一个主要原因是离心作用:即高速转动的板附近的流体产生沿着半径方向向外的速度分量,同时诱发静止板附近的流体向内流动(如图4所示). 对于锥板和平板夹具,雷诺数Re可定义为[41]:

其中h为特征的板间距(平行板h等于间距,锥板h = βR). Turian等研究表明[41],对于利用锥板和平板测试的牛顿流体,实际扭矩T和理想稳定流场下的扭矩T0之比与雷诺数相关:

给定T/T0误差1%,即T/T0 = 1.01,可以得到一个特征的临界雷诺数Recrit=4,该情况下尚未发生持续的湍流. 利用Recrit和剪切速率γ˙=ΩR/h,可以估算锥板和平板稳态剪切的临界条件:

据此我们可以根据实验条件和夹具参数计算出不稳定流场的临界条件. 从公式(14)可以看出,选择较小h的平行板可以抑制二次流,但h过小的时候,两板间微小的不同轴或不平行都会被放大,影响测试的准确性[42]. 因此,需要选择合适的板间距.
为了更直观地展示牛顿流体的二次流不稳定流场对实验数据的影响,图11是我们利用单头应力控制型流变仪MCR-302(Anton Paar)实测的水在剪切速率扫描实验中的黏度相对剪切速率的图,可以看出,在低剪切速率出现的类似于剪切变稀的现象(蓝色区域)可能由于传感器扭矩低于仪器测试下限(Tmin=0.11~0.25 μN·m)或者表面张力的影响,而在高剪切速率下(红色区域),剪切增稠的异常现象是由于板的高速转动引发了二次流.
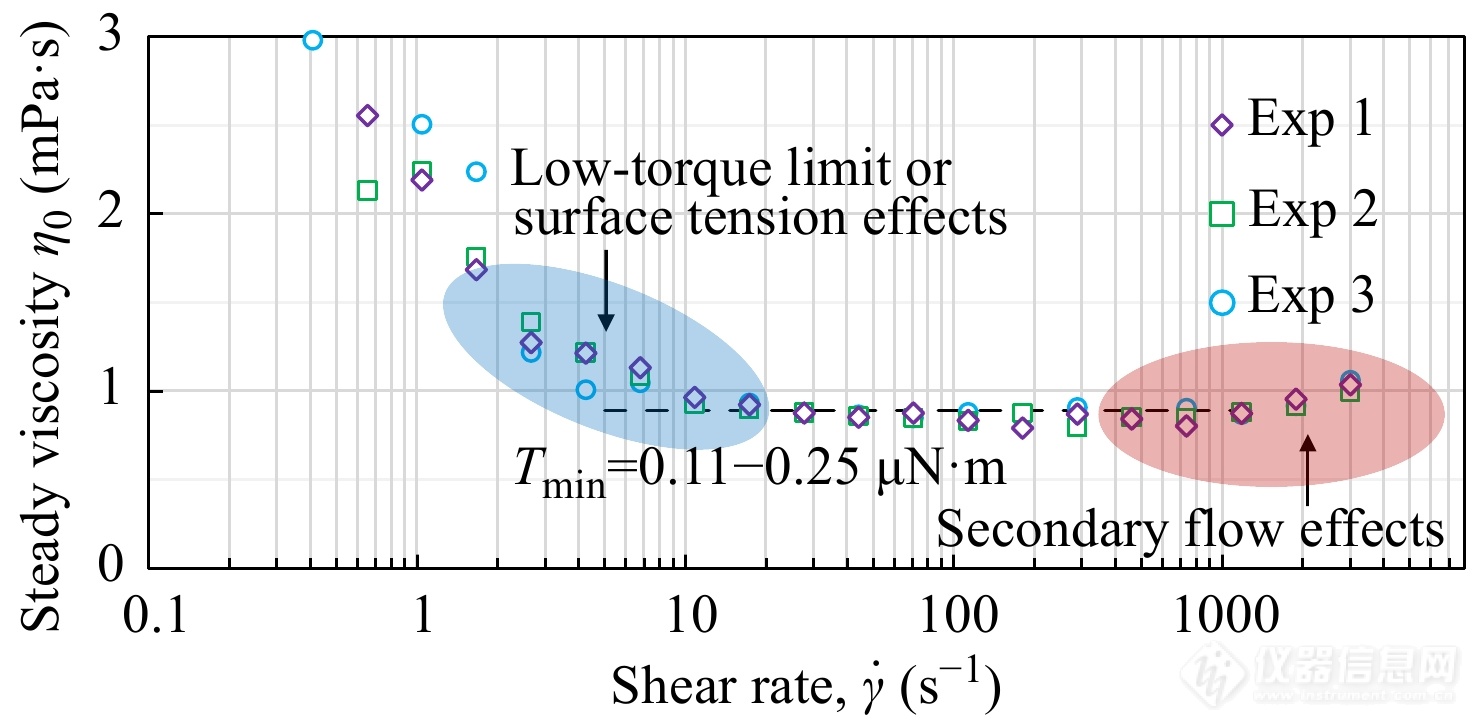
图 11
Figure 11. Steady shear flow measurements of H2O using cone-and-plate with diameter of 50 mm, the scattered plots in the blue regime are obtained from torque below the low-torque limit, the thickening behavior in the red regime is due to secondary flow effect.
3.6 测试中常见问题V:样品表面张力
在使用旋转流变仪测试低黏度的牛顿流体时,表面张力往往会影响到测试结果. 很多低黏度流体异常的实验数据都和其表面张力有关[42,43]. 而表面张力的产生与样品的各向对称程度、样品的自身表面张力以及样品是否存在吸附和聚集有着密切关系[32,44~47]. 为了使读者更加清楚地了解表面张力对流变实验数据的影响,下面我们将分别从样品的各向对称性、样品自身表面张力的大小以及样品自身存在吸附和聚集3种情况阐述表面张力对实验结果的影响.
3.6.1 样品的各向对称性
保证样品的各向对称是流变测试中获得准确实验数据的基础,样品的各向非对称性可能在填充上样时即存在,如过度填充或者填充不足均可造成样品的各向非对称性,各向非对称性也可能在测试过程中产生,如样品的边界在流场下存在一定的形状的波动,或样品不对称的挥发引起样品边缘与板的接触线和接触角的不对称性. Ewoldt等[32,44]研究低黏度样品的剪切流变测试时,发现测试扭矩会受到这些边缘形状变化的影响(如图12所示). 对比完全对称的理想条件,非理想情况下接触线、接触角Ψ(s)和半径都发生了明显的变化. 将接触线看作闭合曲线,可沿闭合曲线积分得到由表面张力引起的扭矩变化. 例如,沿z轴的扭矩Tz可表示为:
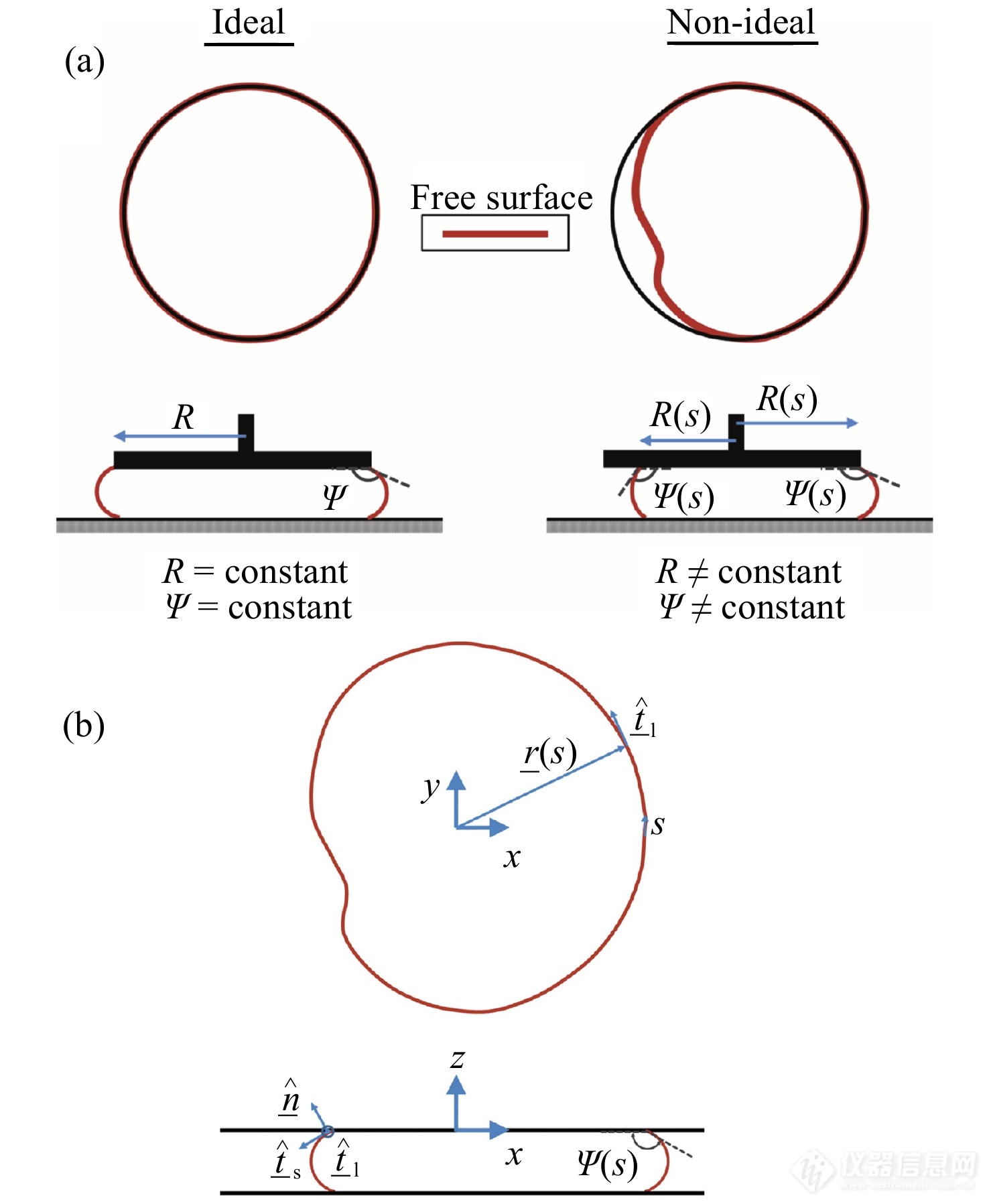
图 12
Figure 12. (a) Contact line and interface angle: ideal versus non-ideal cases. In the non-ideal case, asymmetries are exaggerated compared to typical loading and can also occur as a result of overfilling; (b) Contact line in z=0 plane represented by an arbitrary parametric curve, r–r_(s). (Reprinted with permission from Ref.[44]; Copyright (2013) Society of Rheology).

公式中,r(s)是半径,Γ(s)是表面张力,t^l,r是闭合曲线的切线矢量. 从公式(15)中可知表面张力产生的扭矩与接触线的几何形状、样品的表面张力和界面角均相关. 样品填充不足或过量填充都会导致表面张力引起扭矩增加. 此外,样品挥发也可导致样品填充不足,是高分子溶液或水凝胶体系流变测试过程中最容易忽略的问题.
图13显示了Johnston等[44]研究了随着水分蒸发,样品从填充过度到填充不足过程中扭矩的变化. 他们发现,刚开始填充过度会随着水蒸发而缓解,扭矩先减小并保持了一定时间,之后的样品量继续减小导致样品填充不足,接触线断开,此时产生更大的扭矩,然后扭矩会继续保持,直到在更长的时间再次提高. 出现此现象的原因是水蒸发会同时导致接触线和接触角的改变,从而增加了样品的各向非对称性. 因此,对于溶液体系的测试,需要考虑溶剂挥发、样品填充不足导致表面张力引起的扭矩增加,这些因素会影响测试结果.
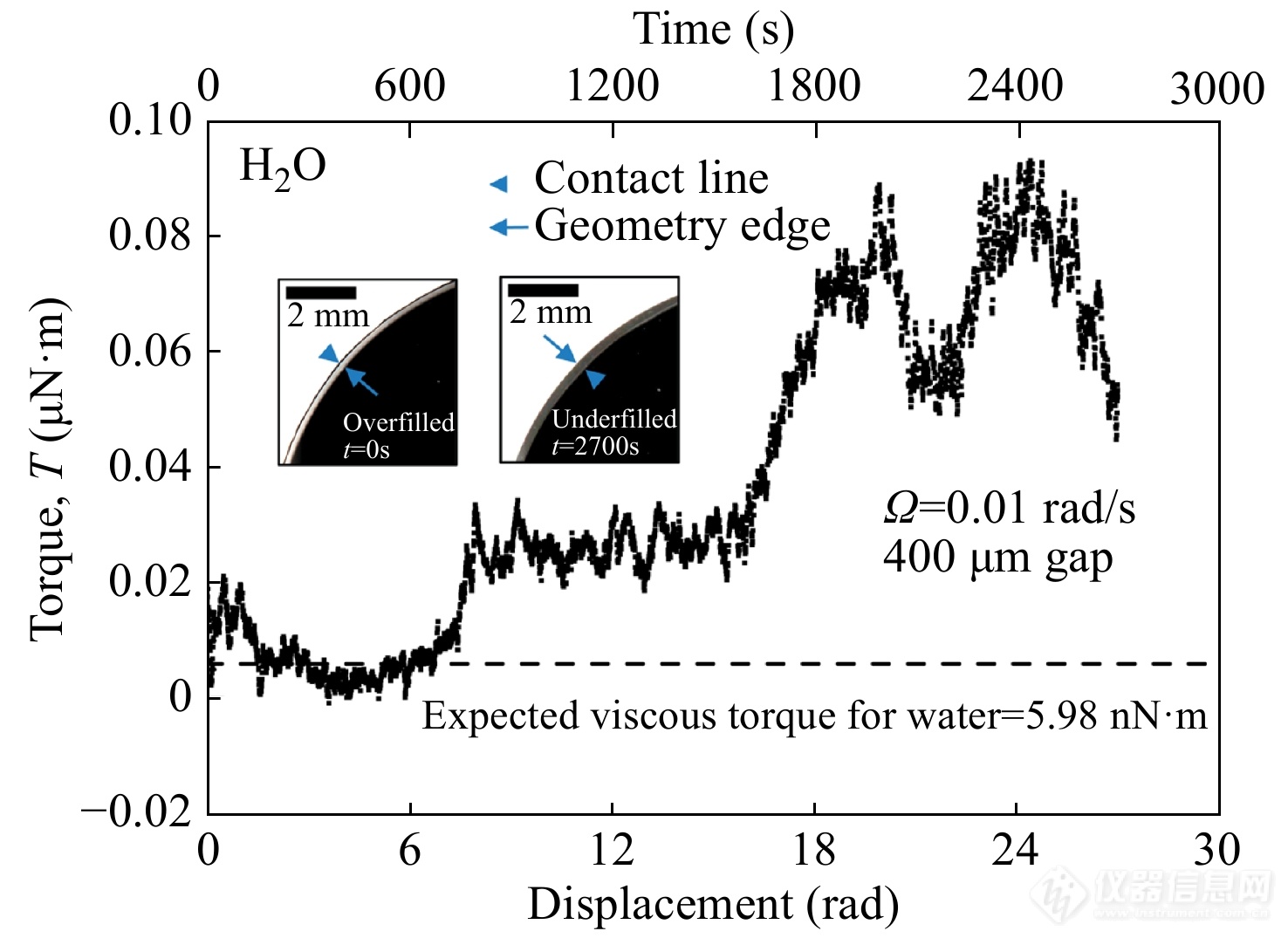
图 13
Figure 13. Evaporation-induced contact line migration, which causes surface tension torque. The geometry is parallel plate (diameter 40 mm) with constant velocity ΩΩ=0.01 rad·s−1. Inset images (views from below) illustrate the contact lines of the overfilled and underfilled cases (Reprinted with permission from Ref.[44]; Copyright (2013) Society of Rheology).
3.6.2 样品本身表面张力大小
样品自身的表面张力的不同也可造成测试结果的显著不同. Johnston等[44]讨论了水和正癸烷在稳态剪切测试过程中测试扭矩与剪切速率的依赖关系,虽然两者室温下的黏度近似,分别为1.17和1.57 mPa·s,利用同轴圆筒测量的低剪切速率下的扭矩却大相径庭,这主要源于水和正癸烷表面张力的不同(75和25.3 mN·m−1),从图14可以看到,相对于正癸烷溶液,具有更高表面张力的水在低剪切速率下显示出由表面张力导致的扭矩平台1 μN·m, 值得注意的是,其中4组水的测试结果表现出该扭矩平台,但仍有2组水的测试结果没有表现出扭矩平台,Johnston 等认为这可能与前面3.6.1节讨论的接触线的不确定性有关.
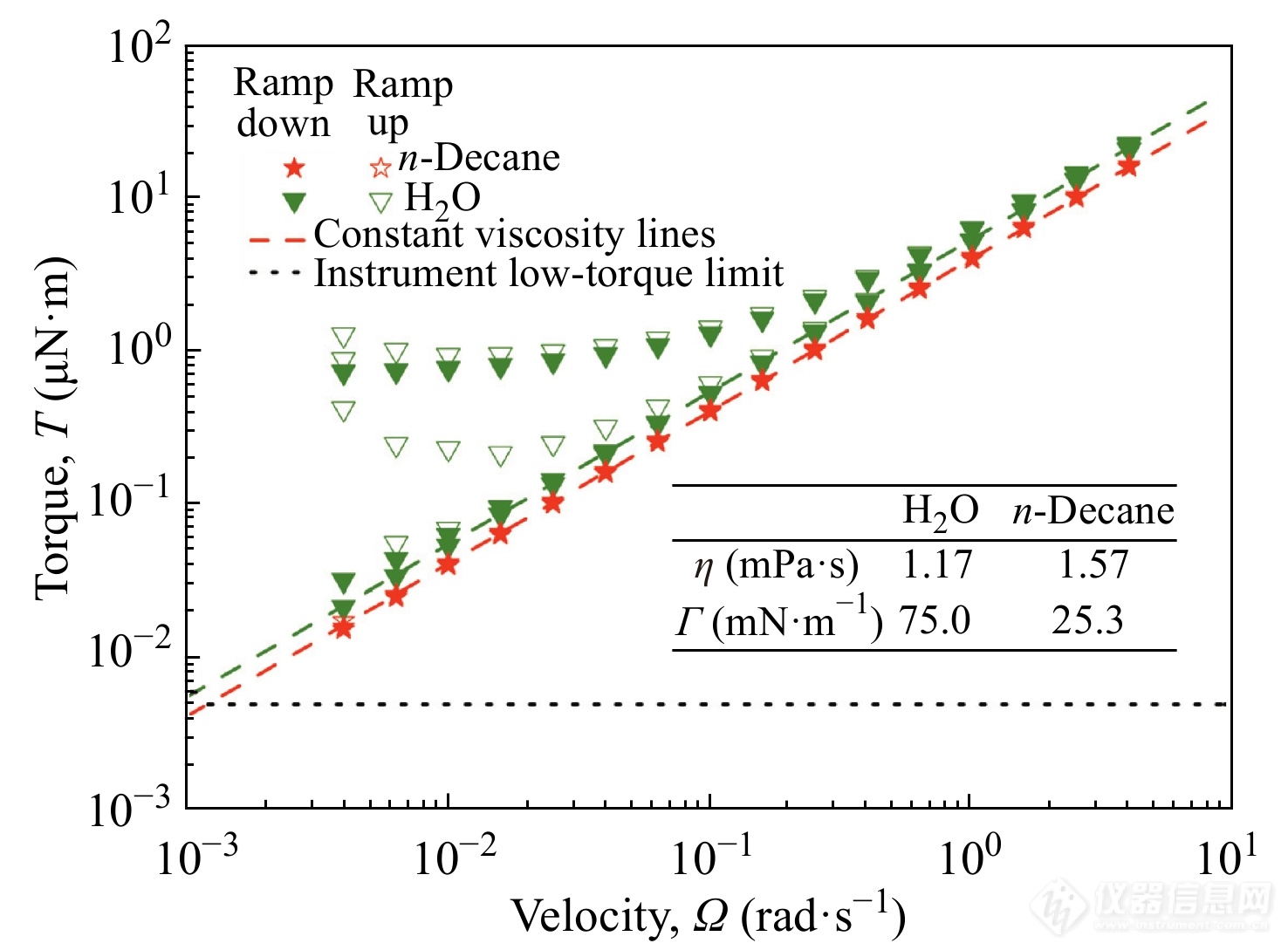
图 14
Figure 14. Steady shear flow with different surface tension (water and n-Decane) using the concentric double gap (DG) geometry (Reprinted with permission from Ref.[44]; Copyright (2013) Society of Rheology)
3.6.3 大分子聚集
对于一些低黏度的蛋白溶液体系,在低剪切速率下的流变测试时,通常需要考虑空气与水界面处形成的蛋白表面膜产生的界面张力和蛋白溶液中蛋白聚集的影响[46,47],表面膜形成和蛋白聚集可导致包括黏度增加、剪切变稀增强和表观屈服应力的出现,这些表面的因素有时会误导研究人员对溶液的整体流动特性的判断. 例如,Castellanos 和Colby等研究了牛血清蛋白和抗体溶液黏度对剪切速率的依赖性[47]. 他们发现:不含表面活性剂成分的牛血清蛋白在液-气界面处形成聚集膜,在低剪切速率下出现明显的表观屈服应力和相应的η∼γ˙−1η∼γ˙−1的屈服区域(图15(a)). 添加表面活性剂能抑制和延缓蛋白表面膜的产生,从而弱化了屈服区域,但经过较长的等待时间(41天),蛋白聚集导致屈服区域逐渐重新形成(图15(b)).
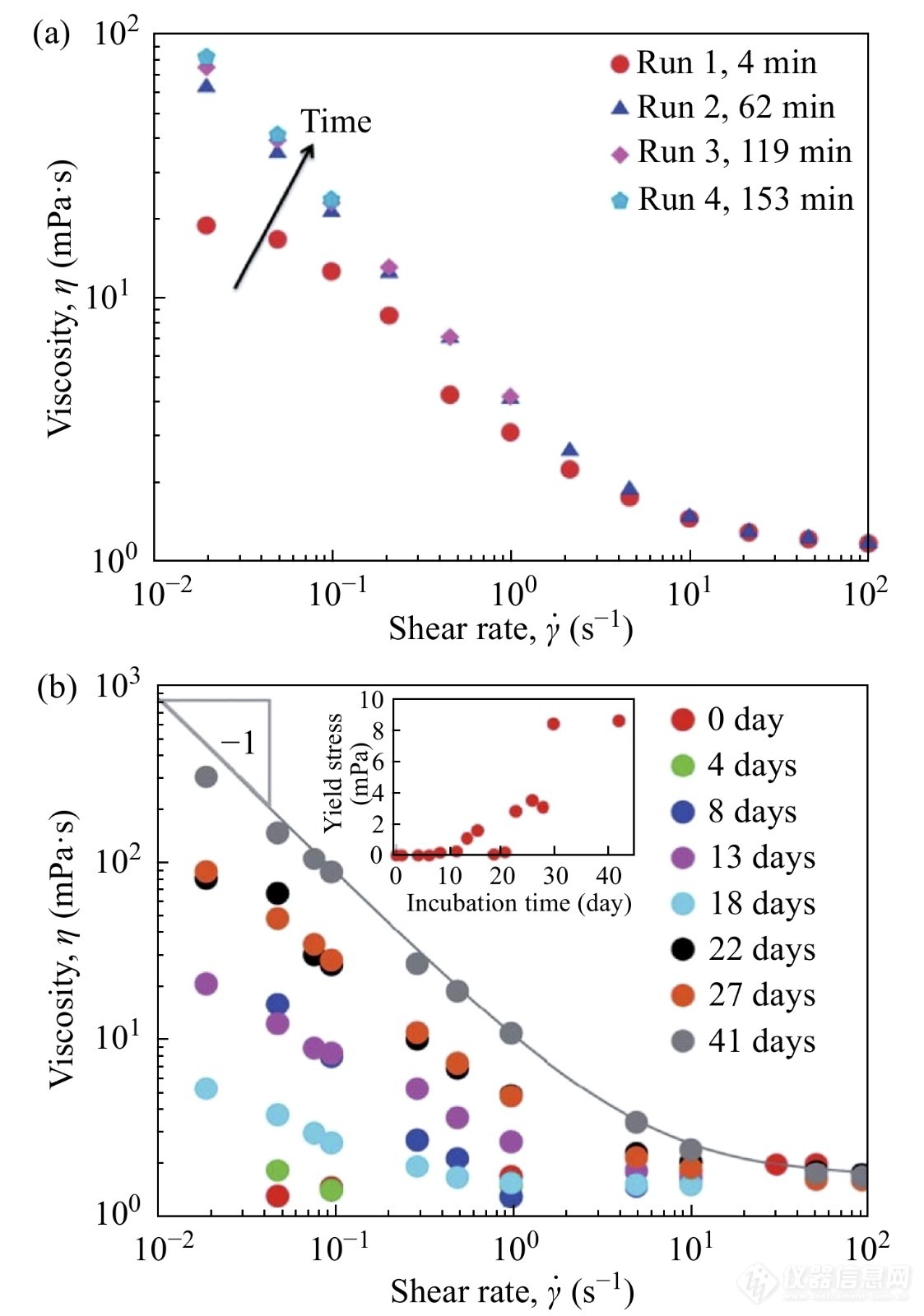
图 15
Figure 15. (a) Increase of apparent viscosity of surfactant-free BSA solutions during the protein aggregation. (b) Increase of viscosity with time, owing to the protein aggregation in the mAb solutions even after introduction of the surfactant. (Reprinted with permission from Ref.[47]; Copyright (2014) The Royal Society of Chemistry)
3.7 测试中常见问题VI: 测试习惯
如上面所述,3个基本假设都是在比较极端的情况下会失效,如样品刚度足够高,需要考虑仪器和夹具柔量的影响;黏度足够低或者剪切强度足够大,需要考虑仪器夹具惯量和样品惯量的影响以及施加流场是否为纯粹的剪切流场. 而在实际流变测试中,也有一些情况满足上述3个基本假设,却得不到准确的测量数据. 下面总结了流变测试过程中一些容易忽略的问题. 为了避免这些问题,提高流变测试的正确性和准确性,需要建立良好的测试习惯.
3.7.1 样品的制备:干燥和挥发问题
对于聚合物熔体,如果样品干燥不充分时,或者测试过程中暴露在湿度较大的环境中,样品中的微气泡和水分会对测试结果产生显著影响,尤其含有氢键和离子极性组分的聚合物(如离聚物),溶剂(如水)对其流变行为的影响明显. 此外,对于水凝胶和溶液体系,测试前和测试过程中需要考虑样品自身溶剂挥发对测试结果的影响,对于溶剂高挥发性的溶液体系这是常见的问题,通常可以使用液封(如用石蜡油密封水溶液)的方法避免溶剂的挥发.
图16展示的是Wolff等[48]对聚二甲基硅氧烷树脂(PDMS)在具有气泡(圆)和无气泡(三角)条件下的频率扫描测试,发现损耗模量几乎不受气泡的影响,松弛末端满足G''∼ω1∼ω1标度关系,而储能模量受气泡影响较大,逐渐偏离G'∼ω2标度关系,这是气泡/样品界面的慢松弛过程导致的.
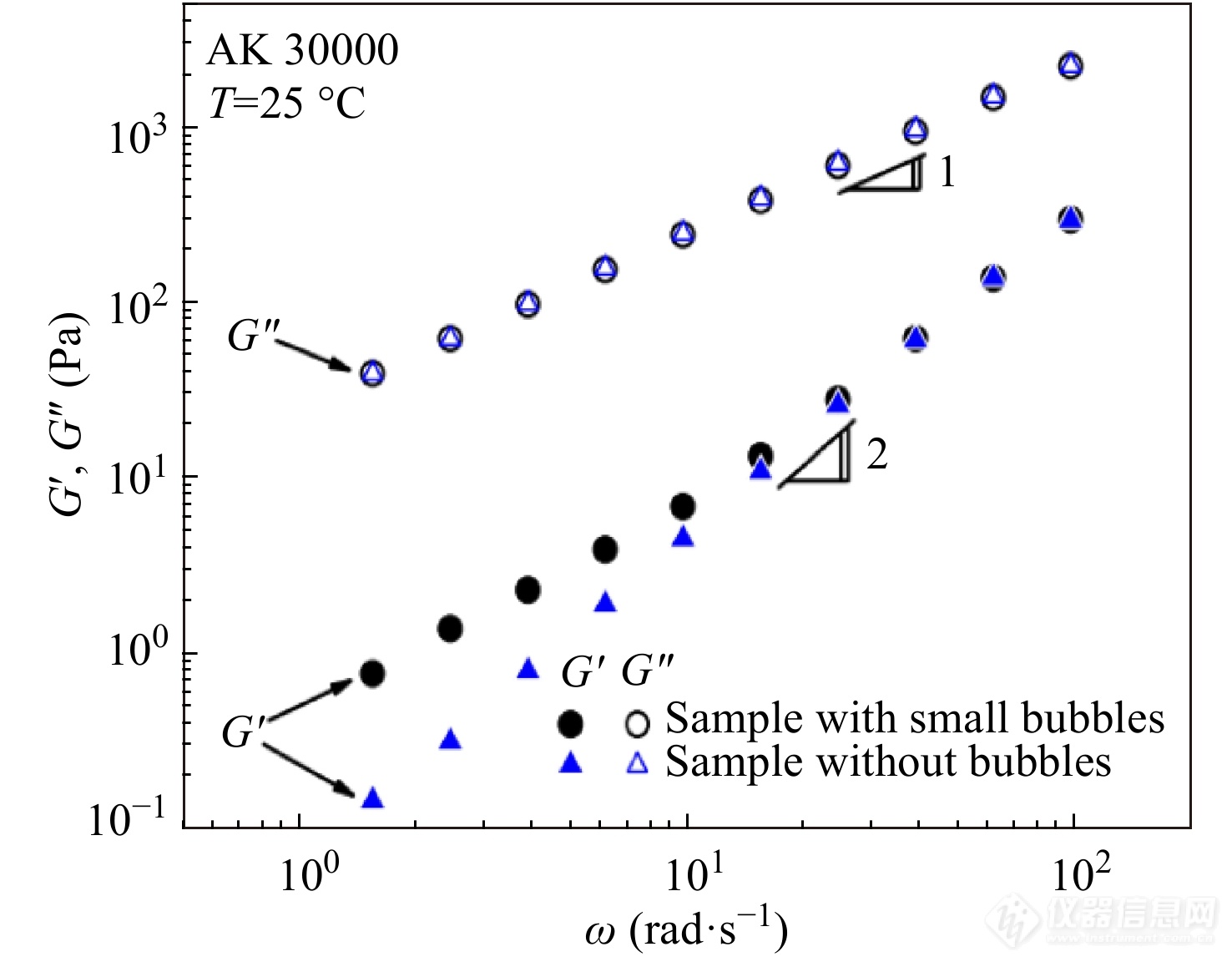
图 16
Figure 16. The storage and loss moduli as functions of the angular frequency for a PDMS silicone oil with and without bubbles (Reprinted with permission from Ref.[48]; Copyright (2013) Spring)
图17展示了Shabbir等[49]对聚四氢呋喃磺酸锂离聚物(PTMO-Li)在干燥和一定湿度条件下的频率扫描测试,他们发现湿度对离聚物的流变性能有很大影响,储能模量和损耗模量相较干燥条件下下降一个数量级左右,由此可见干燥样品对于流变测试的重要性.
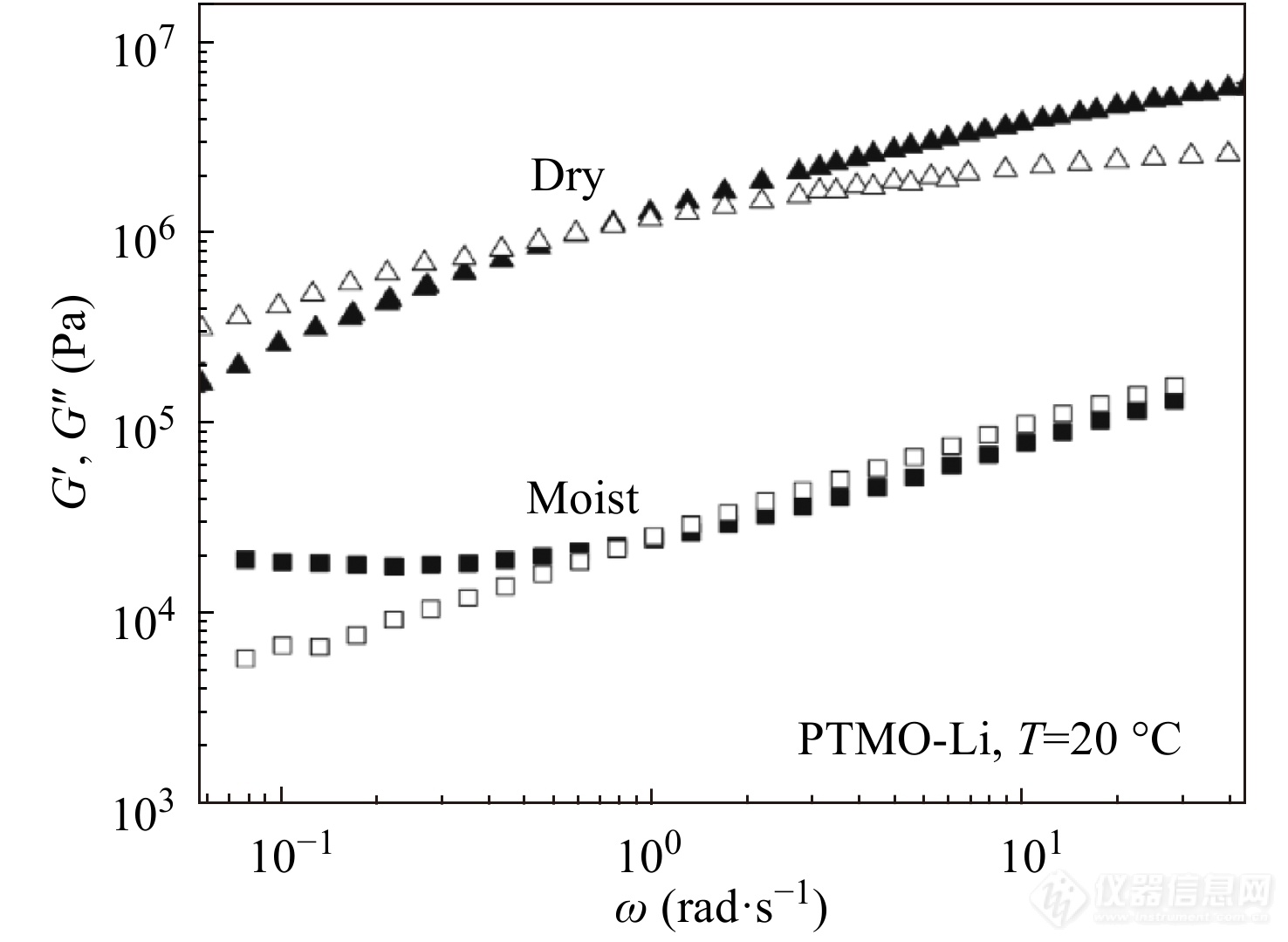
图 17
Figure 17. The storage and loss moduli as functions of the angular frequency for PTMO-Li in dried and undried states. (Reprinted with permission from Ref.[49]; Copyright (2017) Society of Rheology)
3.7.2 确定样品的热稳定性
在进行流变测试之前,对于不熟悉的聚合物样品,需要进行TGA和DSC测试,了解样品的热稳定性和玻璃化转变温度,以便于测试条件的选择,比如:低温测试时样品接近玻璃态,模量接近109 Pa左右,样品较高的模量下突然变化夹具间隙会导致仪器法向力的激增,损坏空气轴承和力传感器;高温测试时,不了解样品热稳定性,测试温度过高会导致样品发生化学交联和降解行为,影响测试结果. 通常,对于容易交联的样品,可以采取添加少量稳定剂的办法抑制化学交联,获取准确的实验数据. 图18展示了Stadler等[50]对低分子量低密度聚乙烯分别在加入少量稳定剂和不加稳定剂条件下,复数黏度随时间扫描变化,可以看出当时间经过4300 s之后,样品黏度突然增加,这主要由于体系中含少量双键的组分发生化学交联导致,而加入少量稳定剂的样品持续到8.24×105 s (~9.5天)后,样品才开始降解,说明加少量稳定剂的办法可以有效抑制样品的化学交联. 此外,为排除样品在测试过程中发生变化,对测试产生的影响,建议完成所有测试后,再次重复第一步测试,通过数据重复性来考察样品是否在测试过程中发生变化,以保证样品数据的可靠性.
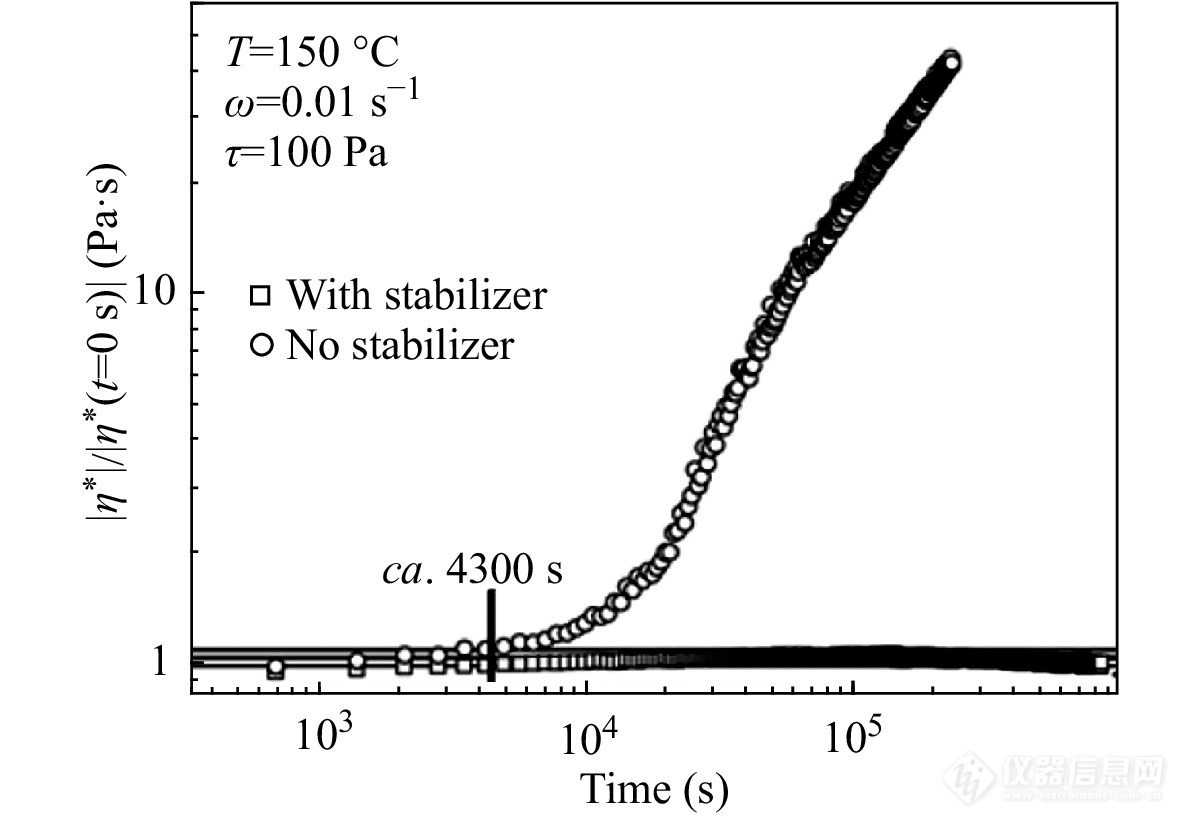
图 18
Figure 18. Thermal instability of sample mLLDPE F18F. The sample without stabilizer exceeds the ±5% criterion after 4300 s owing to the crosslinking, while the sample with stabilizer stays within this criterion for 8.24×105 s (≈9.5 days). (Reprinted with permission from Ref.[50]; Copyright (2014) Springer).
3.7.3 样品体系是否达到平衡态
在测试过程中确保样品体系在测试前是否达到平衡稳态是获取准确数据的前提. 例如超高分子量聚乙烯样品,从结晶状态加热到熔体状态后,往往需要较长时间才能达到链充分缠结的平衡态. 例如,图19展示了超高分子量聚乙烯样品在加热到160 °C熔融后,体系从低缠结状态达到缠结平衡态的过程中储能模量G'的变化,作者发现,热平衡时间随着合成分子的时间(图中标示),也即分子量增加而增加,对于合成30 min的样品,热平衡时间长达约一天之久[51]. 这种缠结程度低于平衡缠结程度的样品也可以通过在稀溶液中沉降高玻璃化温度的长链高分子(如高于缠结分子量的聚苯乙烯)来制备[52,53].
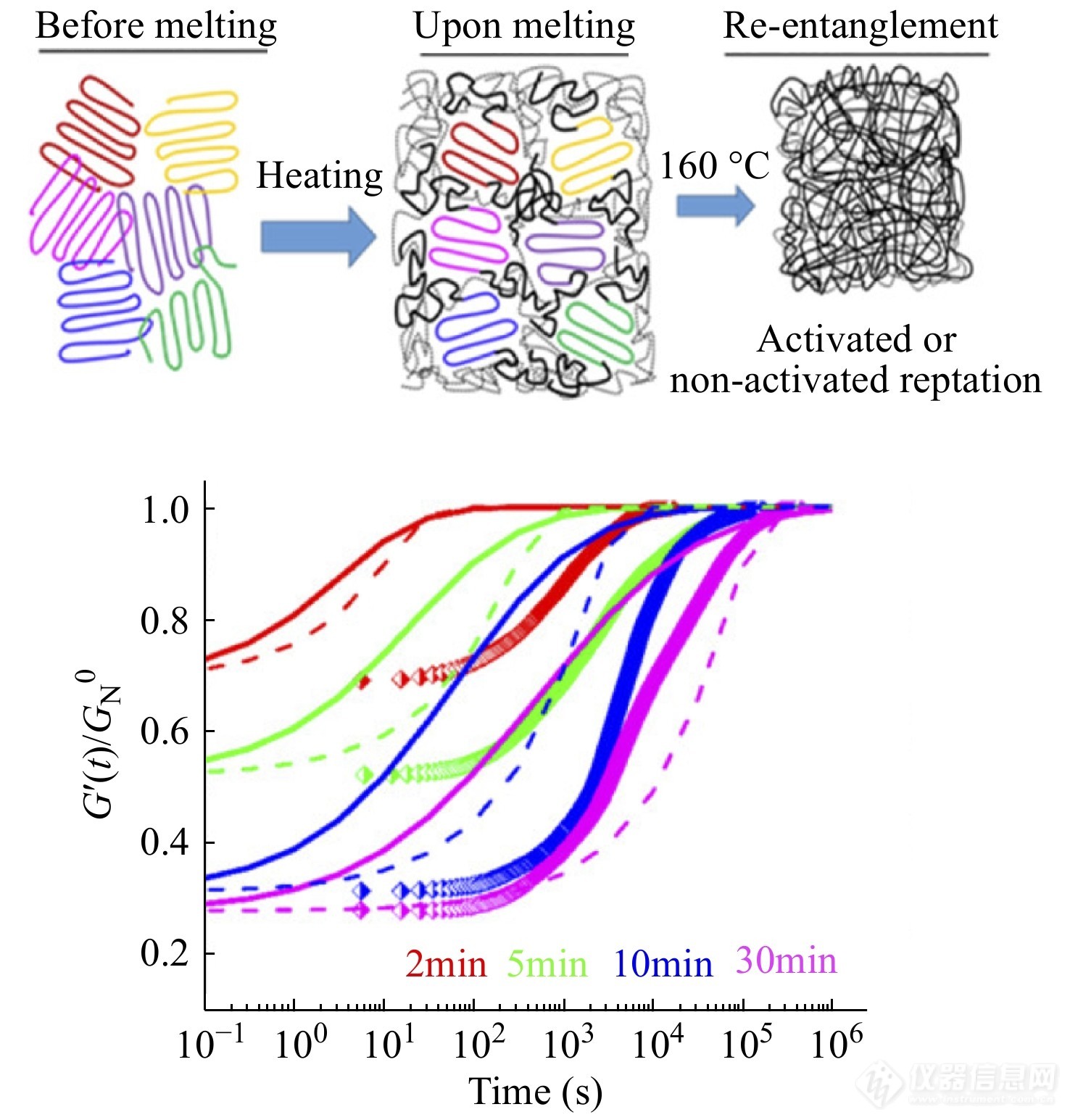
图 19
Figure 19. Buildup of modulus in disentangled polymer melts with time of ultra-high-molecular-weight polyethylene. The top scheme shows the mechanism and the bottom figure shows the measured storage modulus G'(t) against time (symbols), where G'(t) has been normalized by the equilibrium plateau modulus GN0. Curves are the predictions based on tube theory. (Reprinted with permission from Ref.[51]; Copyright (2019) American Chemical Society)
此外,对于高填充体系、不相容聚合物共混物等极难达到平衡态的体系,常需高速施加预剪切,使体系保持初始态的一致性. 需要注意的是,该初始态往往处于非平衡态.
3.7.4 夹具热膨胀对测试的影响
除了前面3.1和3.2节提到夹具柔量和惯量对测试结果的影响,在测试过程中还需要考虑夹具的热膨胀对测试结果的影响,不同材质的夹具具有不同的热膨胀系数. 现在很多仪器在输入夹具类型时已经考虑到热膨胀系数. 但是很多自制的夹具和可抛弃的夹具在使用之前需要人为地测量热膨胀系数并输入. 此外,样品也具有一定的热膨胀系数,因此在测试温度范围很宽时,需要在加热过程中适当增大板间距,在降温过程中适当减少板间距,从而保持样品的填充程度一致.
此外,还需考虑控温组件的结构也会对夹具的传热温度梯度造成影响[54],即使是同一个夹具在不同控温组件下的膨胀系数也是不同的,夹具膨胀系数的差异直接会影响设置夹具间距的大小,尤其在设置夹具间距很小的情况下(如锥板),板受热膨胀可能会使两板直接接触,造成法向应力的激增从而损坏空气轴承和力传感器.
3.7.5 夹具不平行和不同轴对测试的影响
保证夹具的平行与同轴也是获取实验数据的关键. 随着测试夹具频繁使用,以及不小心跌落,非常容易造成夹具不平行和不同轴,这样会导致仪器校零出现误差以及仪器法向力影响测试结果. 因此,在测试中需要注意夹具的正确使用,特别是不要将不使用的夹具立在桌面上或者高处,以防止跌落造成夹具的变形.
4. 结论与展望
本文结合作者多年的流变测试经验,从流场类型和仪器的特征出发,对流变仪进行了简单的分类. 重点阐述了旋转流变仪的工作原理,剪切流变测试的假设条件及其失效的情况,和实际测试中一些不良的测试习惯及其导致的结果.
简言之,流变仪器测试时,只有当输入或输出的应变或应力为施加在样品上的应变或应力,且流场为纯粹的剪切流场时,测试的结果才是可靠的结果. 这些基本前提都是会在一定的测试条件下失效. 我们结合一些实验实例,具体解释了这些假设条件失效的情况,以及在实际流变测试中仪器完全满足基本假设的情况下,一些不良测试习惯对测试的影响,具体总结如下:
(1) 当样品的刚度接近仪器夹具和传感器的刚度时,在样品形变的同时,仪器夹具和传感器也会发生一定的形变,造成样品的真实应变低于仪器设定的应变. 此时,准确校正夹具和传感器的扭转柔量对于样品的测试是非常重要的. 一般的校正过程中考虑夹具和传感器的柔量(或者刚度)为常数. 然而,真实测试中,该柔量也会随着测试条件(如温度)和仪器状态的变化而变化. 因此,从实验操作上来讲,更可行的方法就是选择合适的夹具来增加施加在样品上的应变和因仪器柔量消耗的应变之比.
(2) 当仪器施加恒定的扭矩时,部分扭矩用于加速驱动马达和夹具旋转,当旋转速度达到稳定时候,测试的扭矩才是真实的样品扭矩. 因此,在瞬态和动态等具有加速过程的测试中,当样品反馈的实际扭矩较小时,源于仪器和夹具加速度过程中的惯量贡献会影响到测试结果. 对于单头的旋转流变仪来说,马达和传感器集成在一边,仪器惯量的影响更大. 虽然双头的旋转流变仪具有力反向平衡功能的传感器,可以很大程度上抑制仪器惯量的影响,但是也无法完全消除该影响. 由于仪器的惯量影响与夹具和仪器的状态相关,需要对仪器进行定期的惯量校正.
(3) 在高速振荡测试过程中,样品在往复运动过程中会产生剪切波,当(夹具)板间距与该剪切波波长相当时,样品自身的惯量影响会使得施加样品内部的流场偏离纯粹的剪切流场,造成相位角的变化和相应的测试模量的变化;在高剪切速率时(如稳态或瞬态测试时),流动的不稳定性使剪切流场产生失稳,造成二次流的出现,二次流叠加在剪切流场上会增加仪器测量的扭矩,导致测试中出现“剪切增稠”的假象. 因此,给定的频率范围内选取合理的板间距h是减少样品惯量影响和抑制二次流的关键.
(4) 对于低黏度的牛顿流体,表面张力对实验结果的影响往往会被忽略. 表面张力产生的扭矩大小与样品的各项对称性、样品的自身表面张力以及样品是否存在吸附和聚集有着密切关系. 因此,在低黏度样品测试过程中,建议结合显微工具在线地观测测试过程中样品形状的变化.
(5) 上述四个方面是在样品模量足够高、黏度足够低或者剪切强度足够大的极端情况下,测试中3个基本假设失效的情形. 其实,在实际流变测试中即使仪器完全满足测试需求和基本假设的情况下,流变测试者如果没有养成良好的测试习惯,也会得不到准确的数据. 因此,我们总结了一些常见容易忽略的问题,例如样品干燥和挥发、样品自身热稳定性,样品是否达到平衡态,夹具和样品热膨胀、夹具的不平行不同轴等问题. 我们针对上述容易忽略的问题进行了阐述,希望有助于流变测试的初学者养成良好的测试习惯,了解这些知识对于维护仪器、保护样品以及获取准确的测试数据都是十分重要的. 虽然流变仪器测试过程中会存在上述因素的干扰,但是读者在熟悉流变仪的原理和养成良好的测试习惯的前提下,是很容易判断出实验数据出现问题的“症结”所在,使得流变仪不再成为科研工作中的“黑箱”.
最后需要指出,本文关注的测试手段仅限于剪切流场. 由于拉伸流场较剪切流场难实现,高分子流变学的实验研究多数在剪切流场下进行. 对于加工过程中同等重要的拉伸流场下测试的仪器和研究还在快速的发展之中[15,55~57]. 笔者计划在后续的综述中探讨拉伸测试的仪器原理和测试技巧.
更多精彩内容,请关注:https://www.anton-paar.cn/products/group/rheometer/?utm_source=gongkong&utm_medium=online-ad&utm_campaign=cn_C-00039998_online-portal